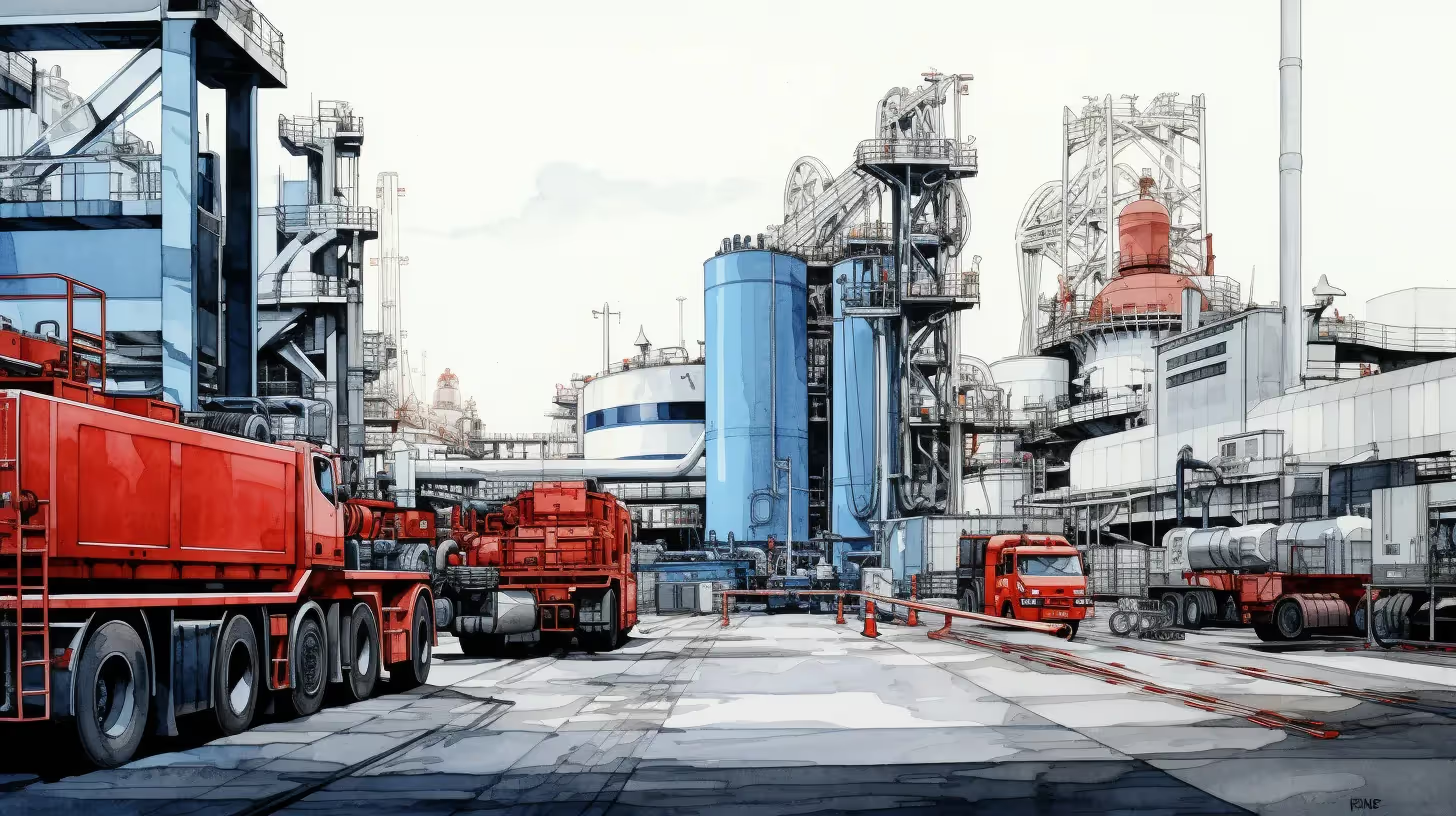
What is Reverse Logistics?
Reverse logistics is a crucial aspect of modern supply chain management that involves the movement of products, equipment, or materials from their final destination back to the manufacturer or service provider. This process encompasses various stages, including returns, repairs, refurbishment, recycling, and disposal. Unlike traditional logistics that focus on the forward movement of goods, reverse logistics deals with the "reverse" flow of items.
Understanding the Process
Reverse logistics addresses the need to manage returned or unused products efficiently. It's a comprehensive approach that considers the entire lifecycle of a product, even after it has been sold and used. This involves tasks such as:
- Returns Management: Handling products that customers return due to defects, dissatisfaction, or other reasons.
- Remanufacturing: Refurbishing and restoring returned products to a like-new condition for resale.
- Repair and Maintenance: Fixing defective items to extend their useful life and minimize waste.
- Recycling: Properly disposing of materials and components that can be recycled to reduce environmental impact.
- Disposition: Managing the final stage of a product's life, whether it's reselling, recycling, or responsible disposal.
The Importance of Reverse Logistics
In today's competitive business landscape, reverse logistics has gained prominence for several reasons:
Sustainability and Environmental Responsibility
Reverse logistics helps organizations minimize waste and reduce their environmental footprint. By refurbishing, recycling, or properly disposing of products, companies contribute to sustainable practices and adhere to environmental regulations.
Cost Efficiency
Effective reverse logistics can lead to significant cost savings. It allows companies to recover value from returned products, reduce inventory carrying costs, and optimize the use of resources.
Customer Satisfaction
Efficient returns and repair processes lead to higher customer satisfaction. Customers who have a hassle-free experience returning or repairing products are more likely to remain loyal to the brand.
Compliance and Regulations
In various industries, regulations and compliance requirements for handling certain types of products, such as electronics or hazardous materials. Proper reverse logistics ensures adherence to these rules.
Maximizing Value Recovery
Reverse logistics enables businesses to extract maximum value from returned products. By refurbishing and reselling items, companies can recapture value that would otherwise be lost.
Conclusion
Reverse logistics is a dynamic process beyond the traditional supply chain, focusing on the "reverse" flow of products and materials. It encompasses various stages, including returns, repairs, refurbishment, recycling, and disposition. The benefits of efficient reverse logistics range from sustainability and cost efficiency to customer satisfaction and compliance with regulations. Organizations that embrace effective reverse logistics can enhance their operations, reduce waste, and positively impact both their bottom line and the environment.
For more information about reverse logistics solutions and how they can benefit your business, visit UCS Logistics.
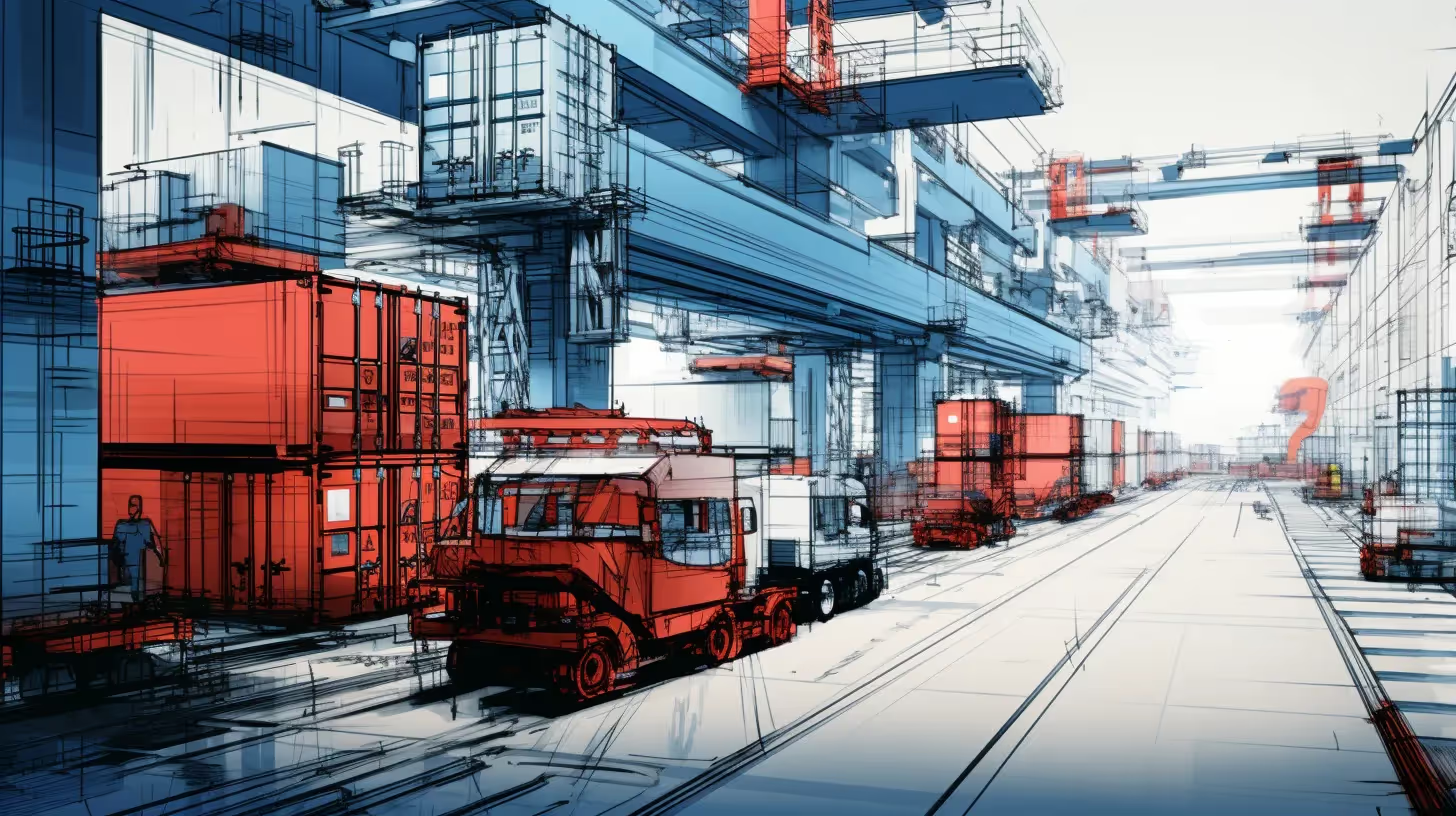
What are the Top Benefits of Reverse Logistics?
Reverse logistics offers a range of benefits to businesses across various industries. These advantages improve sustainability, cost savings, customer satisfaction, and regulatory compliance. Here's a closer look at the top benefits of implementing effective reverse logistics strategies:
Sustainability and Environmental Responsibility
Reverse logistics is vital in promoting sustainability and environmental responsibility. Businesses reduce waste by refurbishing, recycling, and responsibly disposing of products and minimizing their ecological impact. This aligns with modern consumers' growing concerns about eco-friendly practices and can enhance a company's reputation as a responsible corporate citizen.
Cost Efficiency and Value Recovery
Efficient reverse logistics can lead to significant cost savings. By refurbishing and reselling returned products, companies can recover value that would otherwise be lost. Optimizing returns management and repair processes also reduces the financial burden associated with excessive inventory and wasteful disposal.
Enhanced Customer Satisfaction
Smooth and hassle-free returns, repairs, and exchanges increase customer satisfaction. Customers who encounter a seamless reverse logistics process are more likely to remain loyal to the brand and recommend it to others. Positive customer experiences in the reverse logistics realm contribute to overall brand loyalty.
Compliance with Regulations
In electronics, healthcare, and manufacturing industries, there are regulations governing the proper handling of returned products, hazardous materials, and waste disposal. Effective reverse logistics ensures that companies adhere to these regulations, avoiding legal issues and potential fines.
Inventory Management and Reduced Overstocking
Implementing reverse logistics strategies helps organizations better manage their inventory. By accurately assessing returned items and deciding whether to refurbish, resell, or recycle them, companies can prevent overstocking and optimize the allocation of resources.
Data Insights and Continuous Improvement
Reverse logistics provides valuable insights into why products are returned, allowing companies to identify patterns and trends. This information can be used to improve product design, manufacturing, and customer service, ultimately enhancing the overall quality of products.
Brand Reputation and Customer Trust
Efficient reverse logistics positively impacts brand reputation and customer trust. When customers know that a company stands by its products and offers easy returns and repairs, they are more likely to have confidence in their purchases and perceive the brand as reliable.
Maximized Product Lifecycle
Reverse logistics extends the lifecycle of products by enabling repairs and refurbishment. This maximizes the value of products and reduces the need for new manufacturing, contributing to resource conservation and sustainability.
Innovation and Competitive Edge
Companies that excel in reverse logistics often find innovative ways to refurbish and repurpose returned items. This creativity can give them a competitive edge by allowing them to introduce unique, eco-friendly products or services to the market.
Conclusion
Effective reverse logistics offers many benefits to businesses, ranging from sustainability and cost efficiency to enhanced customer satisfaction and compliance with regulations. By embracing well-planned reverse logistics strategies, companies can optimize their operations, improve their bottom line, and contribute to a more environmentally conscious and customer-centric business model.
For more information about how reverse logistics can benefit your business, visit UCS Logistics.
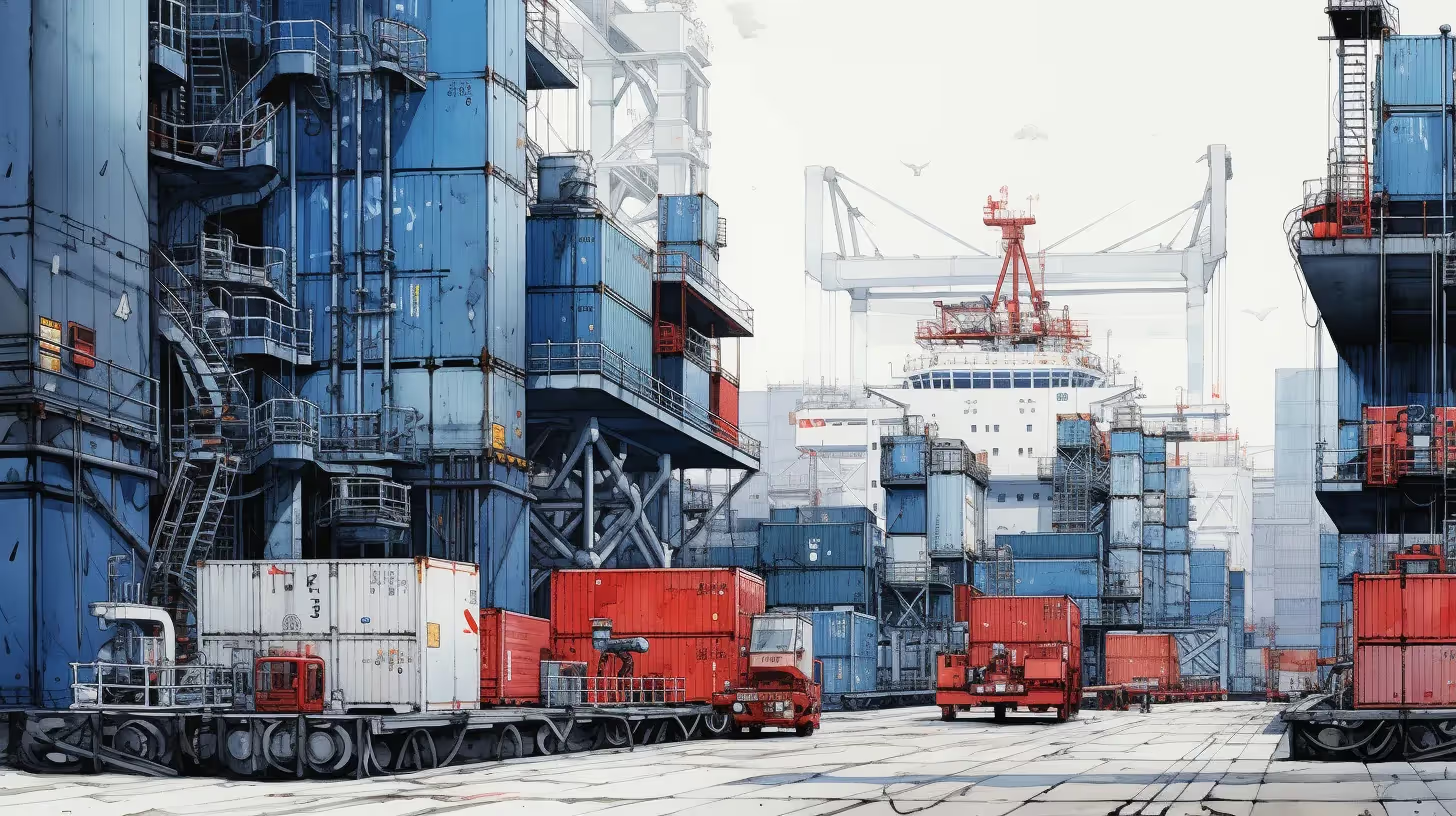
What are the Top Challenges of Reverse Logistics?
While reverse logistics offers numerous benefits, businesses also face certain challenges when implementing effective strategies for managing the reverse flow of products. These challenges can vary depending on the industry, products, and specific business practices. Here are some of the top challenges associated with reverse logistics:
Complex Returns Process
Managing returns involve intricate processes, from verifying the reason for return to assessing the item's condition. Handling various types of returns, such as defective, unwanted, or damaged products, requires careful coordination and efficient systems.
Uncertain Product Condition
Returned products may be in different conditions, from like-new to heavily damaged. Assessing the condition accurately is crucial for determining whether items can be repaired, refurbished, or need to be disposed of.
Inventory Management
Balancing inventory levels in reverse logistics can be challenging. Overstocking or understocking returned products can lead to financial losses and missed opportunities for value recovery.
Disposal and Recycling
Properly disposing of products that cannot be refurbished or resold requires compliance with regulations and environmentally responsible practices. Handling hazardous materials adds a layer of complexity.
Cost Management
Reverse logistics can be costly due to processes such as inspections, repairs, and shipping. Optimizing these processes while keeping costs in check requires strategic planning and resource allocation.
Data Management
Managing data related to returned products, reasons for return, repair processes, and final dispositions can be overwhelming. Efficient data management systems are essential for making informed decisions.
Customer Expectations
Meeting customer expectations for hassle-free returns and quick refunds is vital for customer trust and satisfaction. You must meet these expectations to avoid negative reviews and reduced brand loyalty.
Logistical Complexity
Reverse logistics involves coordinating various parties, including customers, carriers, repair centers, and disposal facilities. Ensuring smooth communication and collaboration among these entities is essential.
Lack of Visibility
Visibility into the reverse logistics process can be limited, making tracking the status of returned products, repairs, and refurbishment difficult. This lack of transparency can hinder decision-making and efficiency.
Integration with Forward Logistics
Aligning reverse logistics with forward logistics operations seamlessly is a challenge. Proper coordination ensures that returned products re-enter the supply chain without disruptions.
Conclusion
Reverse logistics presents businesses with unique challenges that require careful planning and execution. From managing complex returns processes to ensuring compliance with regulations and satisfying customer expectations, these challenges demand strategic solutions. By addressing these obstacles head-on and implementing effective reverse logistics strategies, businesses can unlock the benefits of optimized resource utilization, improved customer satisfaction, and enhanced sustainability.
For more information about how UCS Logistics addresses reverse logistics challenges, visit UCS Logistics.
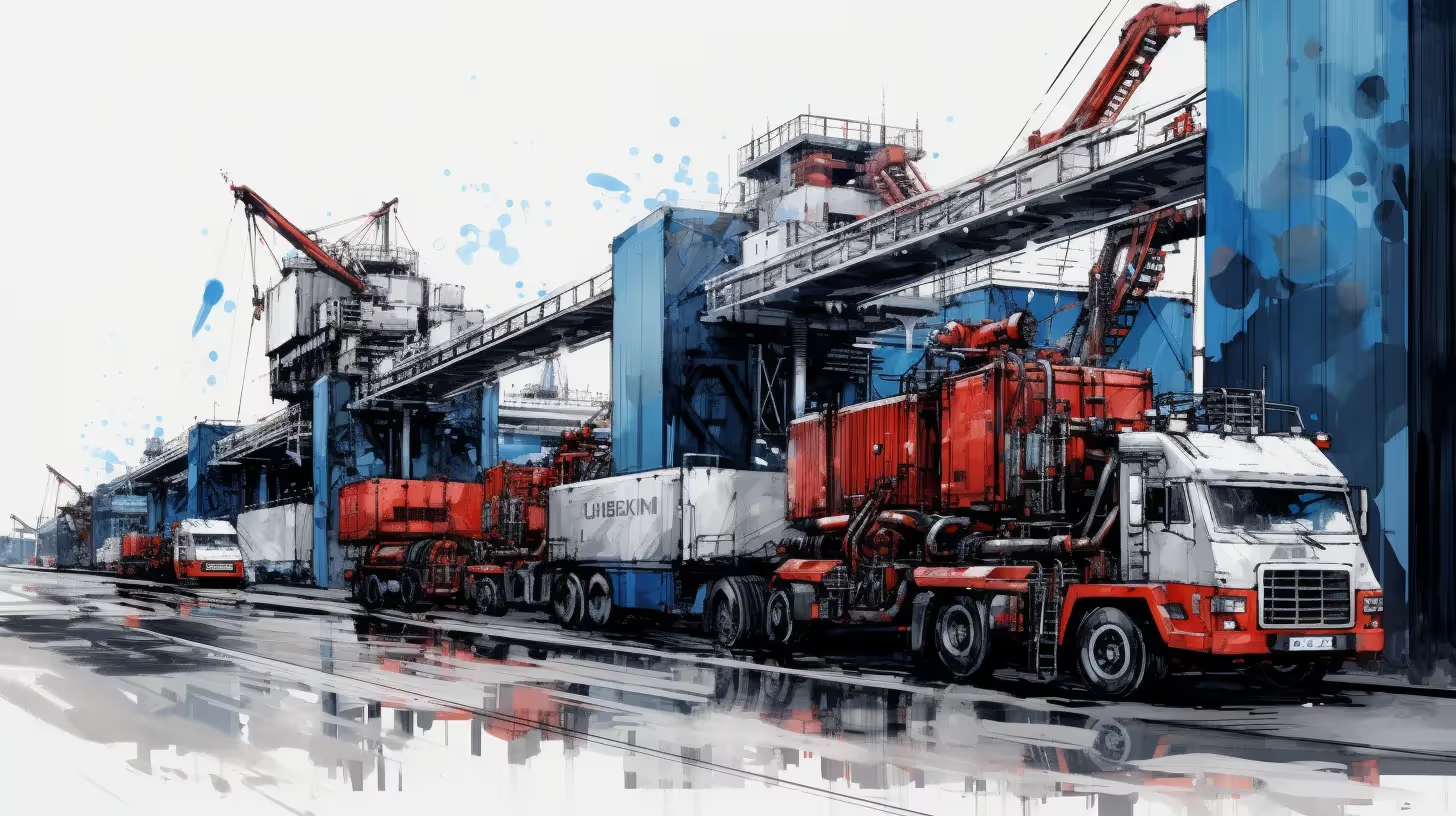
Strategies to Optimize Reverse Logistics
Optimizing reverse logistics processes requires careful planning and strategic implementation. Businesses can address the challenges associated with managing the reverse flow of products by adopting effective strategies. Here are some key strategies to optimize reverse logistics:
Streamlined Returns Process
Implement a streamlined returns process that makes it easy for customers to return products and provides clear instructions for different return scenarios. Simplifying the returns process enhances customer satisfaction and reduces the likelihood of errors.
Advanced-Data Analytics
Utilize advanced data analytics to gain insights into return patterns, reasons for return, and product conditions. Analyzing this data helps identify trends and areas for improvement, enabling more informed decision-making.
Efficient Inspection and Sorting
Invest in efficient inspection and sorting processes to accurately assess returned products' condition. Categorize items based on their potential for repair, refurbishment, recycling, or disposal.
Optimized Repair and Refurbishment
Develop efficient repair and refurbishment processes to maximize return product value recovery. Implement standardized procedures for repairs, ensuring consistent quality and reduced turnaround times.
Inventory Management Tools
Implement inventory management tools specifically designed for reverse logistics. These tools help track returned products, assess their status, and facilitate decisions about their disposition.
Collaboration with Partners
Establish strong collaboration with partners, including carriers, repair centers, and disposal facilities. Effective communication ensures smooth handling of returned products and reduces delays.
Transparency and Communication
Maintain transparency throughout the reverse logistics process. Provide customers with clear information about their returns' status and inform them about repair or replacement timelines.
Compliance with Regulations
Stay up-to-date with regulations governing the handling of returned products and hazardous materials. Ensure compliance to avoid legal issues and maintain ethical practices.
Integrated Systems
Integrate reverse logistics systems with forward logistics operations for seamless coordination. This integration ensures that returned products re-enter the supply chain without disruptions.
Continuous Improvement
Review and refine reverse logistics processes based on performance data and customer feedback. Continuous improvement enhances efficiency and keeps processes aligned with changing business needs.
Conclusion
Optimizing reverse logistics is essential for businesses to effectively manage returned products, minimize waste, and recover value. By adopting strategies such as streamlining returns processes, leveraging data analytics, and collaborating with partners, companies can overcome challenges and reap the benefits of improved sustainability, customer satisfaction, and cost efficiency.
For more information about how UCS Logistics optimizes reverse logistics, visit UCS Logistics.
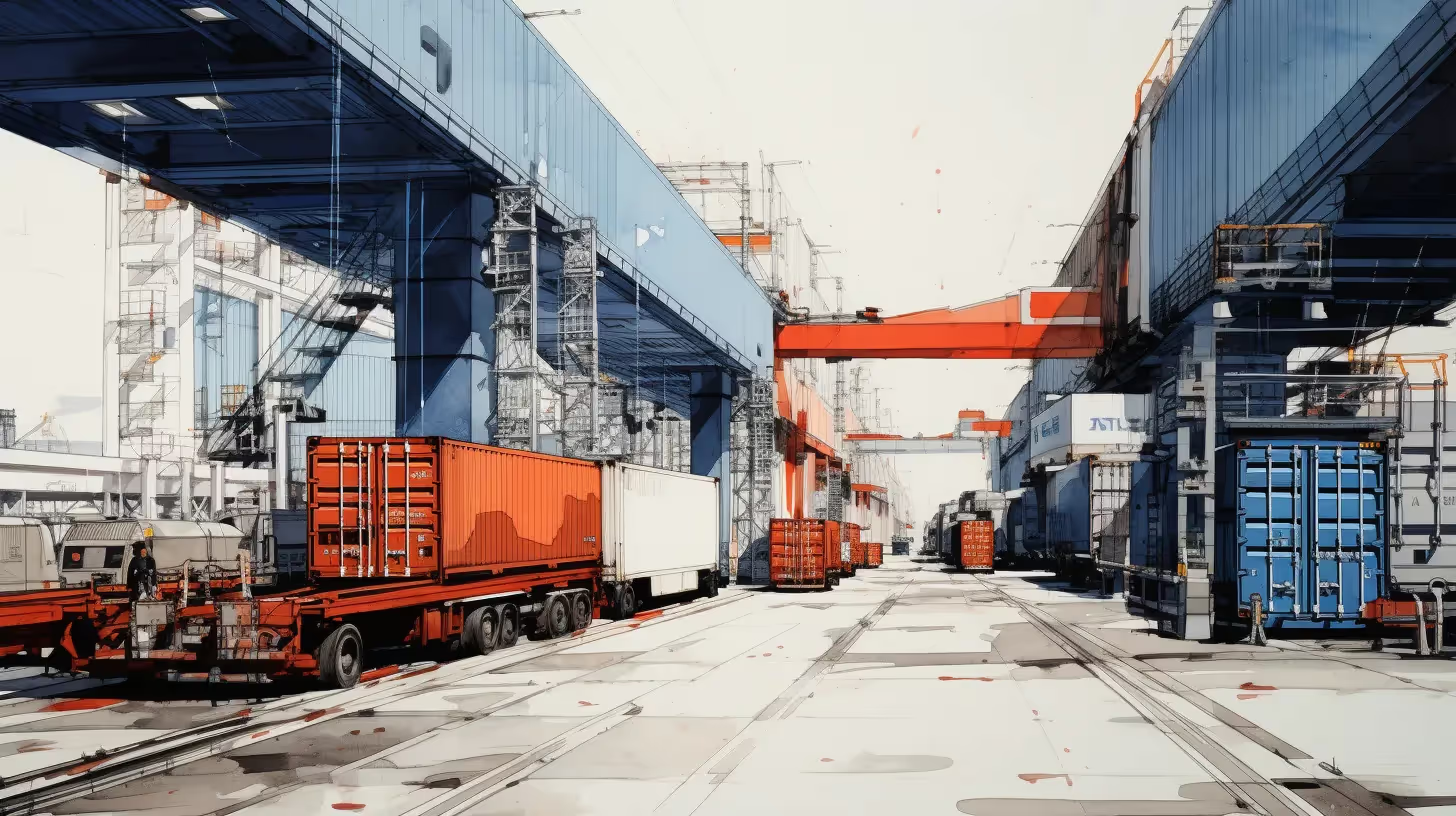
The Benefits of UCS Reverse Logistics for Your Business
UCS Logistics offers a comprehensive suite of reverse logistics solutions tailored to address the unique challenges businesses face in managing the reverse flow of products. Our strategies are designed to optimize processes, enhance sustainability, and drive customer satisfaction. Here's how UCS Reverse Logistics can benefit your business:
Expertise in IT Asset Management
With our extensive experience in IT asset management, UCS Logistics understands the complexities of handling IT equipment, data security, and regulatory compliance. We specialize in managing various equipment types, including end-user devices, data center hardware, and various other hardware.
Efficient Returns and Repairs
Our streamlined returns and repairs processes ensure efficient handling of returned products. We assess the condition of items accurately and implement repairs or refurbishments as needed, maximizing value recovery and reducing waste.
Advanced-Data Analytics
UCS Logistics leverages advanced data analytics to gain insights into return patterns, helping you identify trends and areas for improvement. This data-driven approach enhances decision-making and enables continuous process optimization.
Sustainability and Compliance
We prioritize sustainability and compliance by adhering to environmental regulations and responsible disposal practices. Our solutions help you minimize waste, recycle materials, and meet industry-specific compliance requirements.
Customer Satisfaction
Our commitment to seamless returns and repair processes contributes to enhanced customer satisfaction. We help you maintain customer trust and loyalty by offering hassle-free returns and efficient repairs.
Inventory Management
UCS Logistics assists in efficient inventory management, preventing overstocking or understocking of returned products. Our solutions optimize the allocation of resources and reduce inventory carrying costs.
Integration with Forward Logistics
We ensure smooth integration of reverse logistics with forward logistics operations, enabling returned products to re-enter the supply chain seamlessly. This integration minimizes disruptions and enhances operational efficiency.
Collaboration and Communication
Our strong collaboration with partners, including carriers, repair centers, and disposal facilities, ensures effective communication and coordination. This collaboration results in efficient handling of returned products and reduced processing times.
Continuous Improvement
At UCS Logistics, we believe in continuous improvement. We regularly assess and refine our reverse logistics processes based on performance data and industry best practices, ensuring your business benefits from the latest advancements.
Conclusion
UCS Reverse Logistics offers a range of benefits to businesses seeking efficient, sustainable, and customer-centric solutions for managing returned products. Our expertise in IT asset management, streamlined processes, data-driven insights, and commitment to customer satisfaction make us a trusted partner for optimizing reverse logistics operations.
For more information about how UCS Logistics can benefit your business through our reverse logistics solutions, visit UCS Logistics.
Takeaways from the Article:
- Reverse logistics plays a crucial role in managing the flow of products back to the manufacturer or retailer after sale.
- Effective reverse logistics processes can lead to cost savings, improved customer satisfaction, and environmental benefits.
- Returns management, product refurbishment, and recycling are key components of reverse logistics.
- Embracing technology and data analytics can enhance the efficiency and visibility of reverse logistics operations.
- Collaborative partnerships within the supply chain are essential for successful reverse logistics implementation.
Main Point of the Article: The article discusses the importance of reverse logistics and its benefits in terms of cost savings, customer satisfaction, and environmental impact.