In a world where operational efficiency and cost management are paramount, Maintenance Optimization emerges as a crucial business strategy. It's more than just fixing what's broken; it's about strategically planning and implementing maintenance activities to maximize asset reliability and lifespan while minimizing costs. But how do we navigate the complexities of Maintenance Optimization? What are the best practices, and how can businesses like UCSLogistics.com assist in overcoming these challenges?
Did you know...
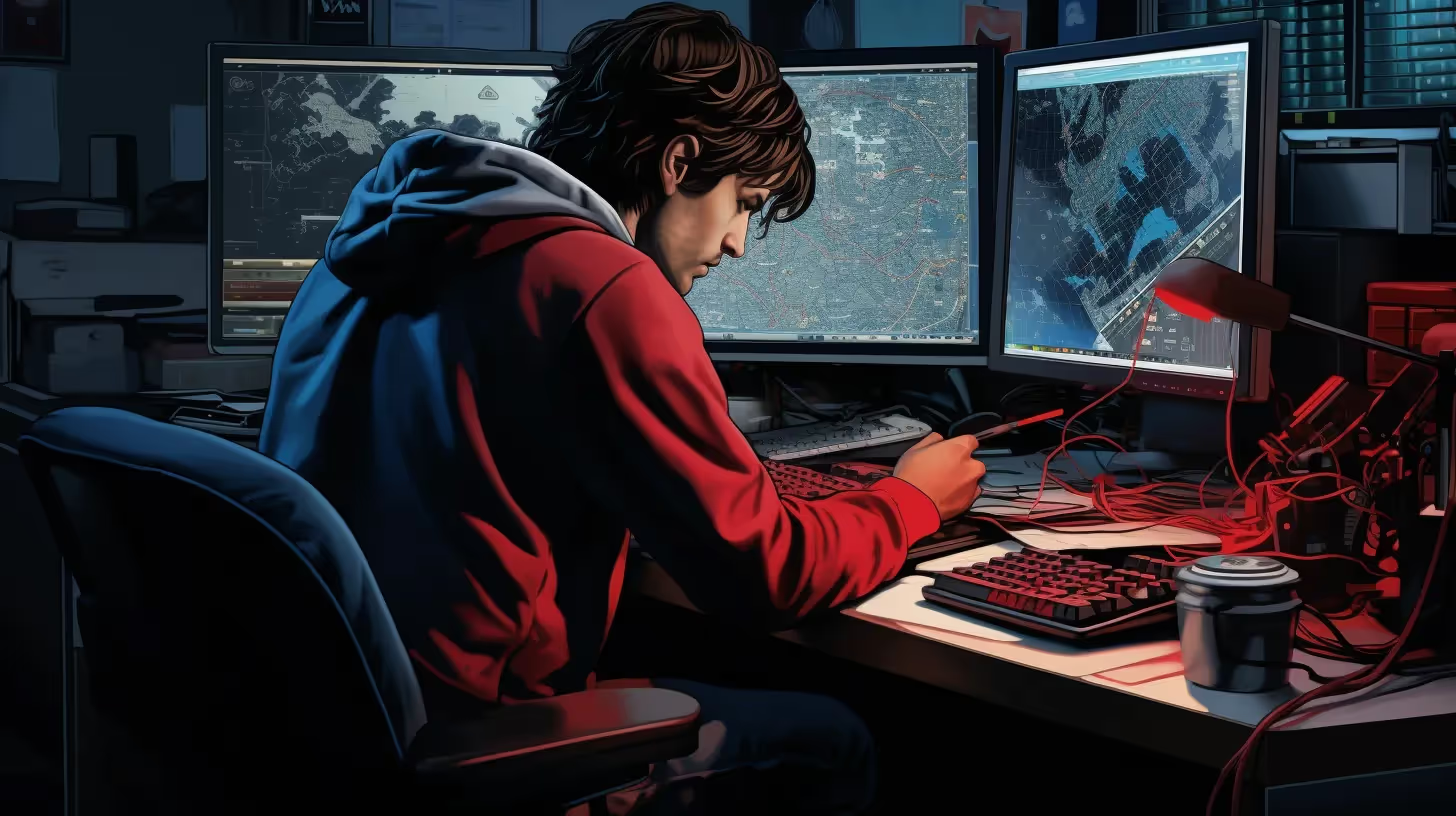
Sub-Topics in Maintenance Optimization
In maintenance optimization, several sub-topics play a critical role in ensuring equipment efficiency and effectiveness. Below is a table outlining these sub-topics:
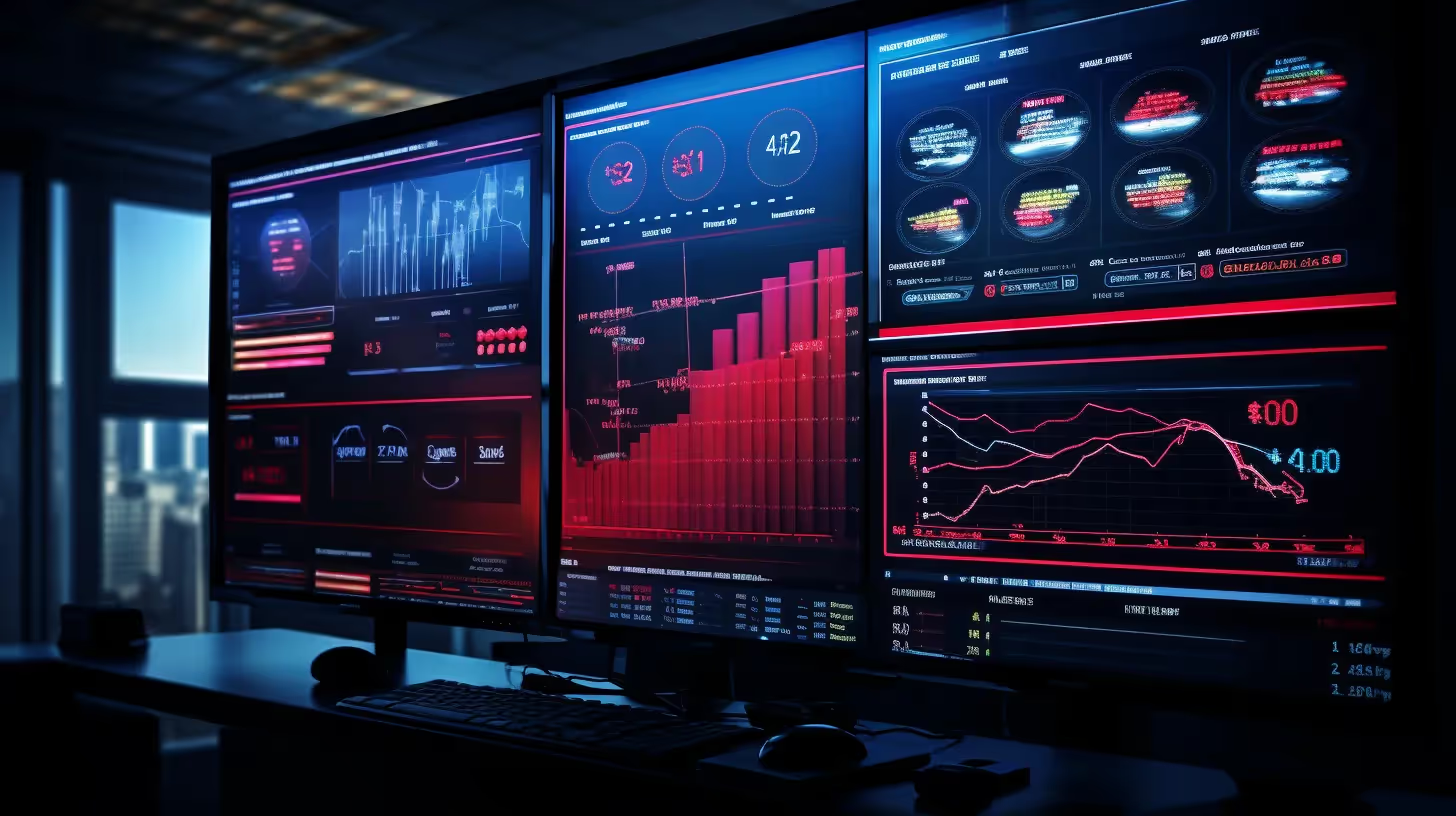
Maintenance Optimization - Definition and Implementation
Defining Maintenance Optimization
Maintenance optimization minimizes downtime and system effectiveness at the lowest possible costs while considering all constraints.
Key Elements of Maintenance Optimization
- Planning and Scheduling: Ensuring short-term maintenance and optimizing long-term strategies.
- Planned Maintenance Optimization (PMO): Improving maintenance strategies based on preventive routines and failure history.
- Efficiency in Execution: PMO leads to more efficient maintenance activities, aligning with Reliability Centred Maintenance (RCM) principles.
Implementing Maintenance Optimization
Steps to Successful Implementation
- Implement Preventive Maintenance: Begin with establishing preventive maintenance strategies.
- Document Equipment Details: Record details like equipment make/model and condition.
- Leverage Technology: Use digital solutions for scheduling and managing maintenance tasks.
- Develop Effective KPIs: Establish key metrics to measure performance.
- Build Maintenance Checklists: Track KPIs and assess program effectiveness.
- Continuous Improvement: Regularly analyze data to optimize preventive maintenance.
The Three-Phase PMO Process
- Data Collection: Gathering and tracking critical data.
- Data Analysis and Recommendations: Analyzing data to identify and address critical issues.
- Agreement and Execution: Assigning accountability and monitoring progress.
Ensuring Cost-Effectiveness and Efficiency
- Workforce Optimization: Balancing customer satisfaction, service levels, and operational costs.
- Training and Development: Continual employee training to enhance professional competencies.
Creating a Comprehensive Maintenance Plan
- Goals and Priorities: Define clear goals for your maintenance plan.
- Proactive Scheduling: Optimize workflow and resource availability.
- Key Performance Indicators (KPIs): Set and monitor KPIs for the maintenance plan.
The Role of Training in Maintenance Optimization
- Continuous Learning: Implement ongoing training opportunities, especially in technology, to enhance employees' skills and experience.
Building an Effective Maintenance Strategy
- Stakeholder Involvement and Consistent Effort: Engage stakeholders, leverage technology, and commit to consistent analysis and improvement.
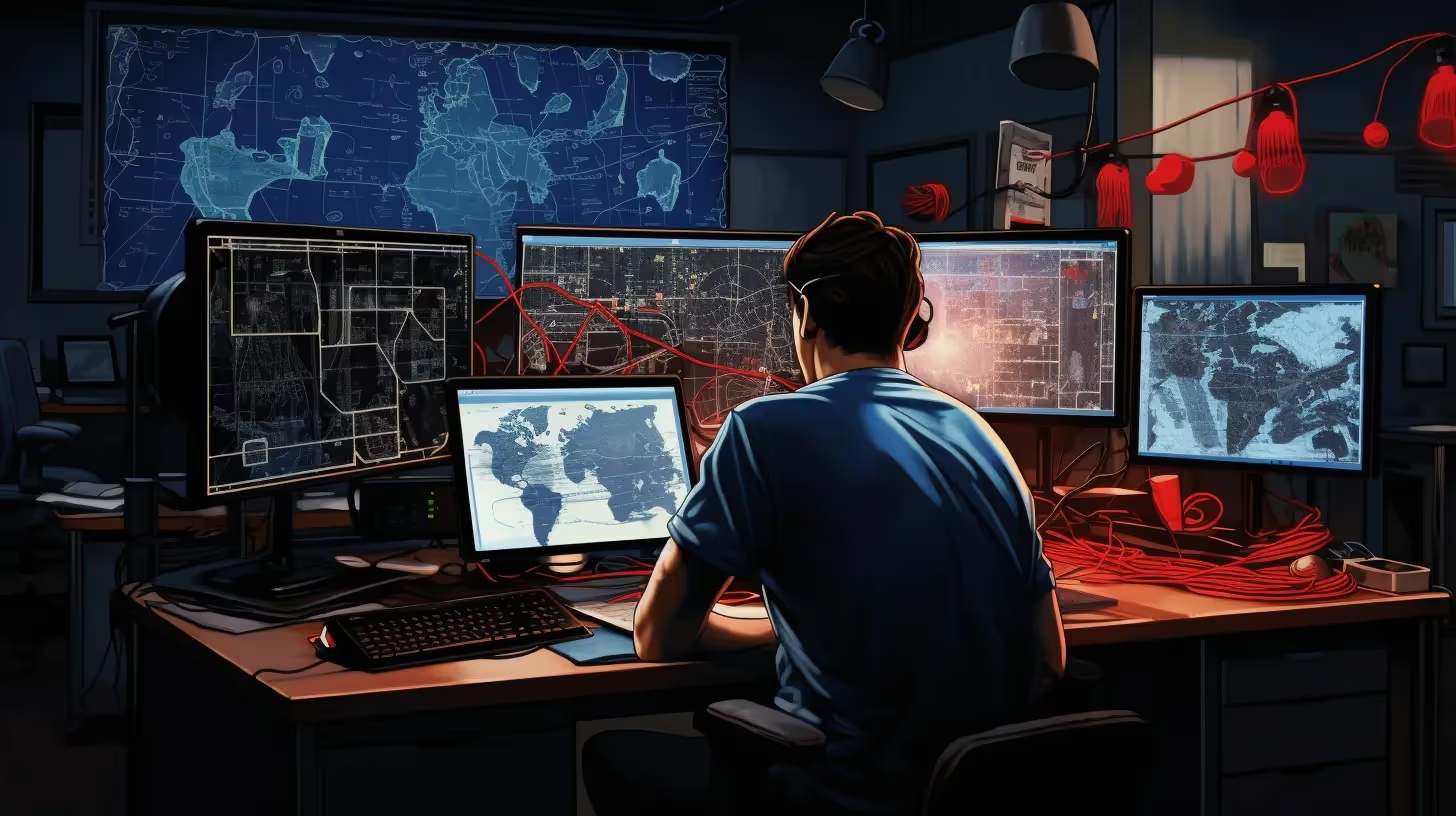
Challenges in Maintenance Optimization
Navigating the Complex Terrain of Maintenance Optimization
Business Challenges in Maintenance Optimization
- Reducing Costs by Eliminating Unnecessary Work: A critical aspect involves minimizing efforts on obsolete or aging assets and streamlining maintenance tasks.
- Adopting Advanced Maintenance Strategies: Transitioning to strategies like Reliability Centered Maintenance (RCM), Safety Integrity Level (SIL), and Risk-Based Inspection (RBI) poses significant challenges.
- Integrating IIoT: Implementing the Industrial Internet of Things (IIoT) effectively into maintenance processes.
Planning and Maintenance Data Challenges
- Complex PM Data: Disorganization in planning and maintenance data can lead to resource allocation inefficiency and difficulty complying with regulations.
- Frequent vs. Necessary Maintenance: Balancing the frequency of maintenance with actual needs is challenging, as over-maintenance can be as detrimental as under-maintenance.
Data Management Difficulties
- Complexity in SAP PM and IBM Maximo: Navigating through complex data structures in these systems is challenging. Maintenance strategies in these systems require careful management of overlapping and interrelated data.
- Preventive Maintenance Strategy: Scheduling preventive maintenance demands thoroughness to avoid overscheduling, which can increase costs counterproductively.
Conventional Approach Challenges
- Risks in System Changes: Altering a live production system for maintenance optimization is risky and time-consuming. This necessitates testing in a staging platform before implementation.
- Challenges with EAM: Implementing changes in the Enterprise Asset Management (EAM) system is difficult due to the need for data compliance and the risk of human error.
Common Challenges Faced by Maintenance Managers
- Reliability of Equipment: Aging equipment and compatibility issues increase downtime and costs. Effective preventive maintenance programs can mitigate these issues.
- Proper Use of CMMS: Ensuring personnel understand and utilize Computerized Maintenance Management Systems (CMMS) is a significant challenge. Adequate training is crucial for effective use.
- Budget and Resource Constraints: A major hurdle is balancing effective maintenance activities within limited budgets and resources. Risk assessments can help in making informed decisions about maintenance activities.
- Team Competency: The skills gap, especially due to the retirement of experienced professionals, poses challenges. Introducing competency management frameworks and training programs can address this issue.
- CMMS Data Quality: Maintaining data integrity in CMMS systems is challenging. Creating guidelines for data entry and providing training can help ensure data quality.
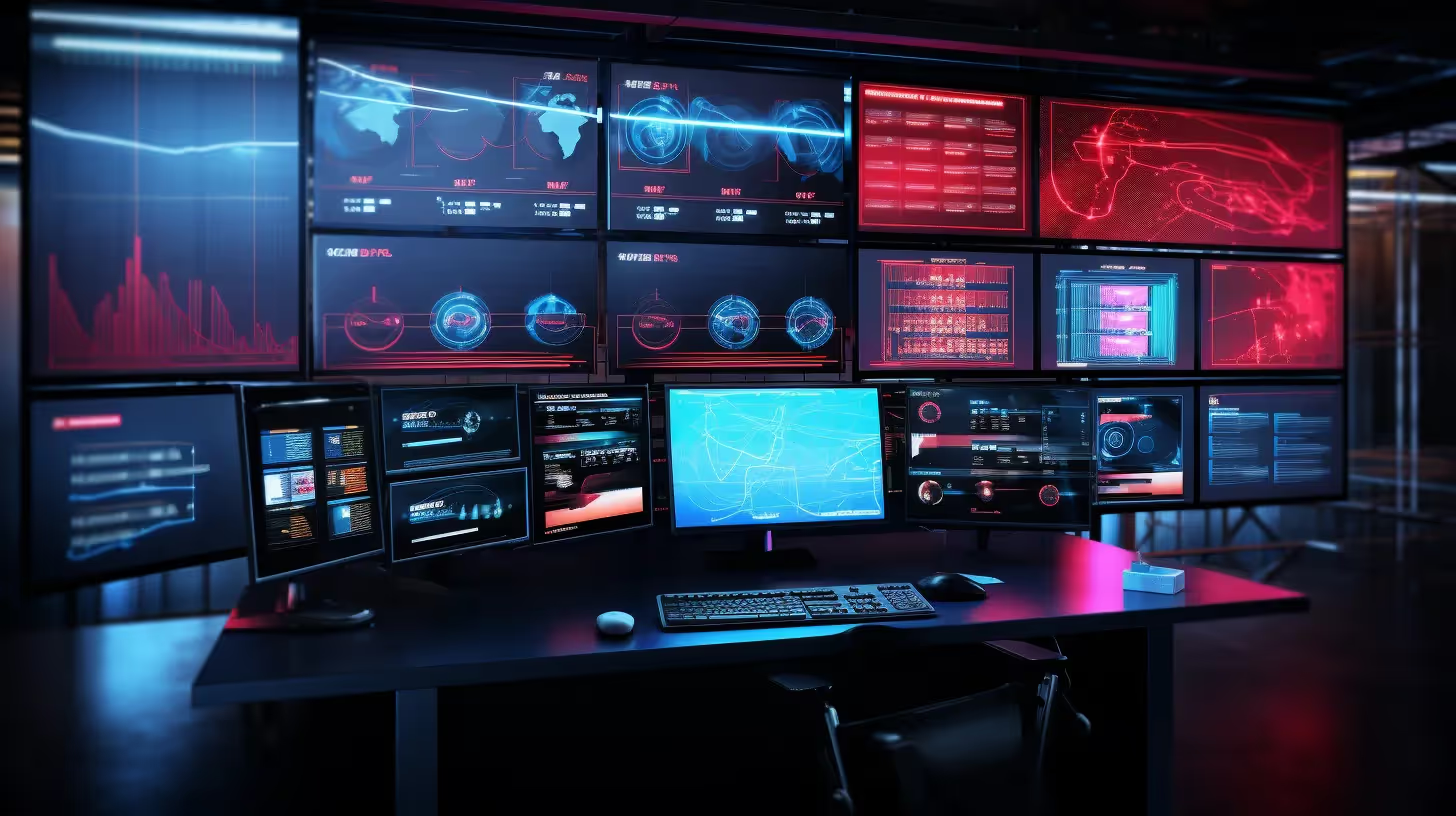
Steps to Success in Maintenance Optimization
Step 1: Educate and Align Your Team in Proactive Maintenance
- Focus: Educate key stakeholders in maintenance and reliability best practices, including preventive and predictive maintenance, root cause analysis, and maintenance cost management.
- Goal: Align everyone on maintenance objectives and strategies for effective implementation.
Step 2: Assess the Current State of Your Maintenance Process
- Process: Involve all stakeholders in assessing the effectiveness of the current maintenance program.
- Approach: Ensure everyone involved understands proactive maintenance to provide consistent and accurate assessments.
Step 3: Create a Master Plan
- Method: Utilize the Crawl, Walk, Run methodology to implement changes gradually but effectively.
- Objective: Start with quick wins and progress to more comprehensive changes that fully integrate the plan.
Step 4: Measure the Impact of the Plan
- Tool: Utilize a Maintenance Scorecard to track and display the performance and impact of maintenance activities.
- Visibility: Post the scorecard in critical areas to keep everyone informed and engaged.
Step 5: Define Roles and Responsibilities
- Implementation: Identify stakeholders to classify roles and responsibilities for all maintenance processes.
- Method: Use the RACI (Responsible, Accountable, Consulted, Informed) Process to define involvement and communication strategies.
Step 6: Host Weekly "Toolbox Talks"
- Format: Conduct brief, 30-minute sessions led by the maintenance supervisor or technicians, focused on maintenance topics.
- Engagement: Encourage learning and sharing knowledge to align with the company's asset reliability goals.
Step 7: Offer Certification Preparation Training
- Opportunity: Provide training in Maintenance and Reliability, such as CMRP and CMRT certifications.
- Benefits: Enhance career development, increase confidence in maintenance decisions, and improve job effectiveness.
Leveraging RCM Framework for PM Optimization
- Approach: Apply Reliability-Centered Maintenance (RCM) concepts as a framework for PM optimization.
- Benefit: Reduces the number of ineffective PMs, enhances understanding of equipment failures, and leads to more effective proactive maintenance tasks.
Implementing Checklist Results
- Precision: Write tasks precisely, considering specific failure modes and inspection frequencies.
- Example: Measure and proactively replace components based on predetermined failure thresholds.
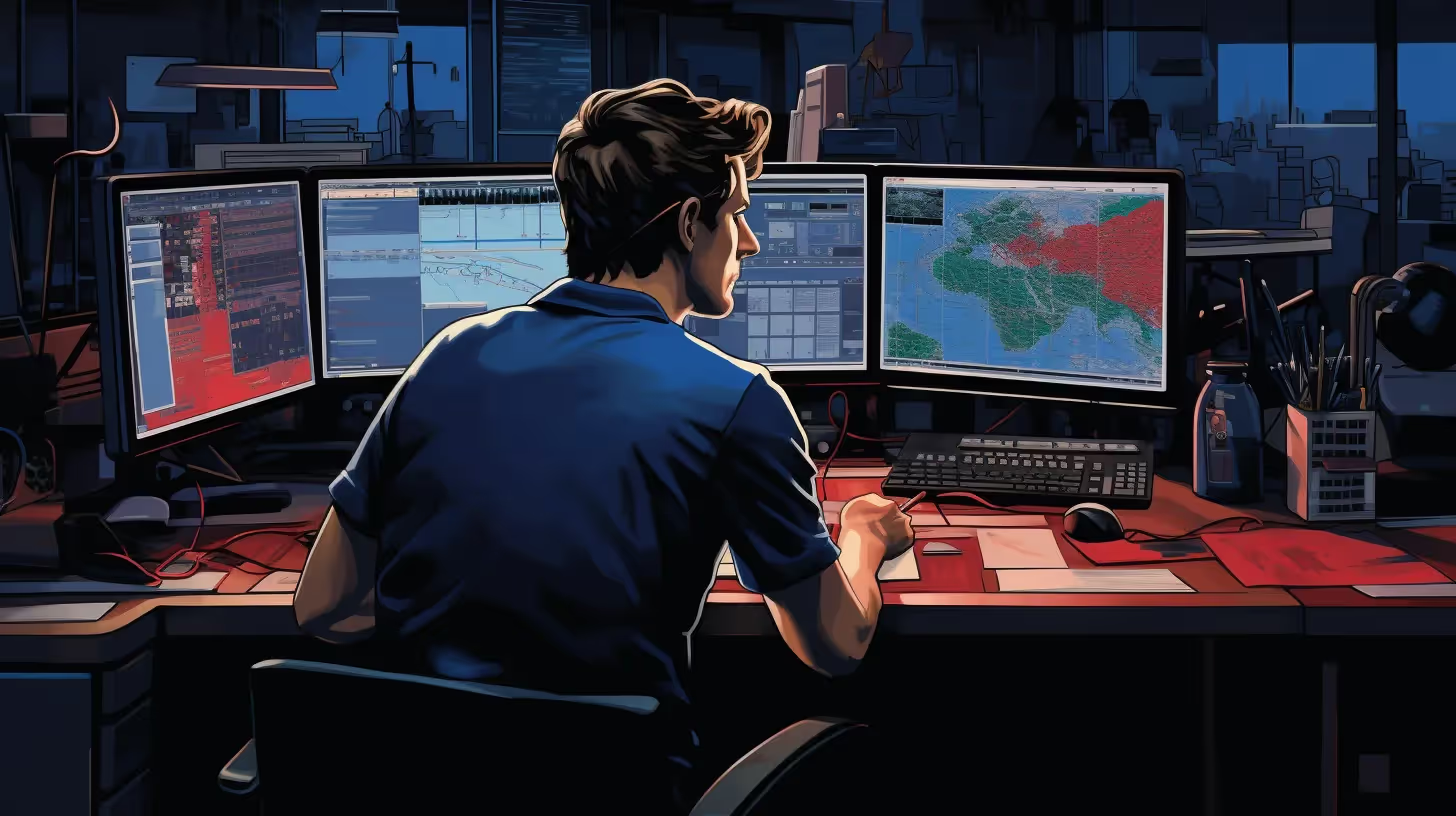
How UCSLogistics.com Assists with Maintenance Optimization Challenges
UCSLogistics.com: Enhancing IT Asset Management and Maintenance
UCSLogistics.com is pivotal in optimizing maintenance, particularly in IT asset management. Their approach encompasses several key aspects:
Computer Repair Service Management
- Efficient Handling: UCSLogistics.com efficiently manages repair processes, scheduling, and tracking to optimize IT asset performance.
- Specialized Software: They utilize computer repair management software to streamline the repair process, ensuring timely resolutions and enhanced customer satisfaction.
Service Management Tools
- Centralized Platform: Service management tools provide a centralized platform for managing service requests, incidents, and assets, enabling better coordination and resource allocation.
- Repair Scheduling Software: This software aids in creating and managing repair schedules, improving technician productivity and response times.
Workflow and Maintenance
- Streamlined Workflows: Workflow management tools define standardized repair processes, reducing manual intervention and human errors.
- Proactive IT Asset Maintenance: They focus on proactive maintenance to minimize repair issues and extend the lifespan of IT assets.
Tracking and Automation
- Service Tracking Systems: Real-time visibility into repair request statuses is provided, ensuring transparent communication and adherence to timelines.
- Automation in Management: Automation features are utilized to streamline tasks like ticket assignments and status updates.
Data-Driven Decision Making
- IT Repair Service Analytics: These tools enable the analysis of repair data to identify trends and make informed decisions, continually optimizing repair processes.
Impact on Business Efficiency and Productivity
- Minimizing Downtime: Efficient management ensures prompt IT issue resolutions, minimizing downtime and boosting employee productivity.
- Cost Optimization: By identifying recurring issues and making data-driven decisions, UCSLogistics.com optimizes costs and manages the IT asset lifecycle effectively.
Additional Strategies for Improvement
- Comprehensive Service Management Tools: Investing in these tools enhances repair process management, from service requests to tracking and technician management.
- Centralized Repair Service System: Establishing a centralized platform improves efficiency and coordination.
- Preventive Maintenance: Regular schedules for preventive maintenance identify and address potential problems early, reducing downtime.
Collaboration for Enhanced Capabilities
- Partnering with Specialized IT Asset Management Companies: UCSLogistics.com collaborates with specialized IT asset management companies to offer comprehensive solutions for streamlining repair processes and optimizing overall IT asset management.
Through these methods, UCSLogistics.com addresses the challenges of maintenance optimization, particularly in the IT sector, contributing to enhanced organizational efficiency and productivity.
Takeaways from the Article
Importance of Maintenance Optimization: It aims to minimize downtime and optimize system use at the lowest costs, considering all constraints.
Planned Maintenance Optimization (PMO): PMO improves maintenance strategies based on preventive routines and failure history, leading to more efficient maintenance activities.
Challenges in Maintenance Optimization: Implementing effective maintenance strategies can be complex due to unforeseen circumstances disrupting planned activities.
Steps for Effective Implementation: These include defining goals, leveraging technology, developing KPIs, and building checklists for continuous improvement.
Efficiency in Execution: PMO aligns with Reliability Centred Maintenance (RCM) principles to lead to more efficient maintenance activities.
Business and Data Management Challenges: These include reducing costs by eliminating unnecessary work, adopting advanced maintenance strategies, integrating IIoT, managing complex PM data, balancing maintenance frequency, and ensuring data quality in CMMS systems.
Reminder of the Post’s Main Point: The main point of the article is the significance of Maintenance Optimization as a strategic approach to enhance operational efficiency and cost management by planning and implementing maintenance activities to maximize asset reliability and lifespan while minimizing costs.