In the dynamic construction world, where every task and resource matters, leveraging technology is crucial for efficiency and success. Construction Equipment Software (CES) is a pivotal tool that enhances operations, streamlines processes, and maximizes resource utilization. This article explores how CES contributes to optimizing construction operations, ultimately leading to successful project outcomes.
Real-Time Equipment Visibility
One of the primary benefits of CES is real-time equipment visibility. Integrated with GPS and RFID technology, CES provides construction companies with accurate, up-to-the-minute location data for each piece of equipment. This real-time tracking eliminates the need for manual checks and offers insights into equipment availability.
Streamlined Maintenance Management
Maintenance is a critical aspect of construction equipment management. CES simplifies maintenance management by automating maintenance schedules and sending alerts for upcoming tasks. This proactive approach ensures that equipment remains in optimal working condition, reducing the risk of unplanned downtime.
Data-Driven Decision Making
CES generates comprehensive data and analytics on equipment performance, utilization rates, and maintenance costs. This data empowers construction managers to make informed decisions regarding equipment allocation, usage patterns, and maintenance schedules. Data-driven decisions lead to efficient resource allocation and cost savings.
Efficient Resource Allocation
CES optimizes resource allocation by analyzing project requirements and equipment availability. By ensuring that the right equipment is allocated to the right tasks, construction companies enhance operational efficiency and avoid delays caused by equipment unavailability.
Minimized Downtime and Delays
Unplanned equipment downtime can lead to project delays and increased costs. CES minimizes downtime by enabling proactive maintenance and quick response to breakdowns. Timely maintenance ensures equipment is ready for use, contributing to uninterrupted project progress.
Compliance and Documentation
Construction projects are subject to regulatory requirements and safety standards. CES aids in compliance by generating detailed maintenance records, inspection reports, and safety logs. This documentation keeps construction companies compliant and simplifies audits and inspections.
Cost Control and Budgeting
CES monitors maintenance costs, fuel consumption, and operational expenses. This data enables construction managers to create accurate budgets and control costs throughout the project lifecycle. Efficient resource allocation leads to cost savings and optimized spending.
Enhanced Equipment Utilization
Optimizing equipment utilization is essential for cost-effective operations. CES analyzes equipment usage patterns, identifying underutilized assets. This insight allows construction companies to allocate equipment more effectively, minimizing waste and maximizing efficiency.
Scalability and Adaptability
As construction projects evolve, CES adapts to changing needs. It accommodates the addition of new equipment, the expansion of job sites, and the growing demands of projects. Scalability ensures that CES remains a valuable asset as construction operations expand.
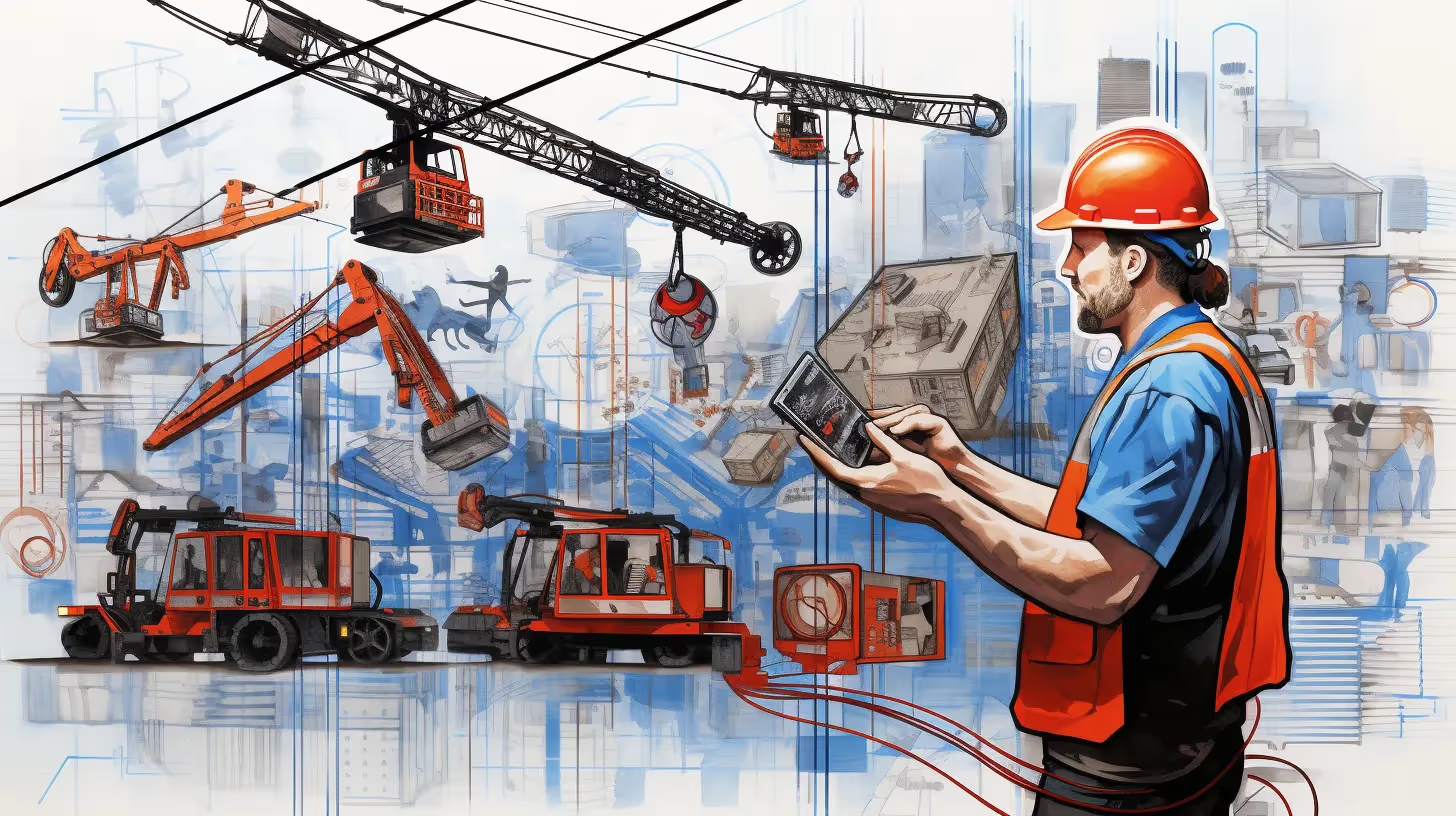
What is Construction Equipment Management?
At its core, construction equipment management involves overseeing, coordinating, and optimizing all equipment used throughout various construction projects. This includes everything from excavators, bulldozers, and cranes to smaller tools like jackhammers and welding equipment. Construction equipment management aims to ensure that the right equipment is available at the right time, in the proper condition, and in the right location to support project tasks effectively.
Efficient Allocation and Utilization: Construction equipment management encompasses procurement, allocation, maintenance, tracking, and retirement. It involves determining which equipment is needed for a specific project, how it will be used, and ensuring it's used to its fullest potential.
Lifecycle Management: Effective equipment management covers the entire equipment lifecycle, from initial acquisition to disposal. This involves managing equipment during active construction and considering storage, maintenance, and future usability.
Cost Control: Managing construction equipment efficiently contributes to cost control. Proper maintenance schedules, preventive measures, and timely repairs can extend equipment lifespan, reducing the need for frequent replacements.
Operational Efficiency: Construction projects can run more smoothly when equipment is well-managed. Delays due to equipment breakdowns or unavailability can be minimized, improving project timelines and overall efficiency.
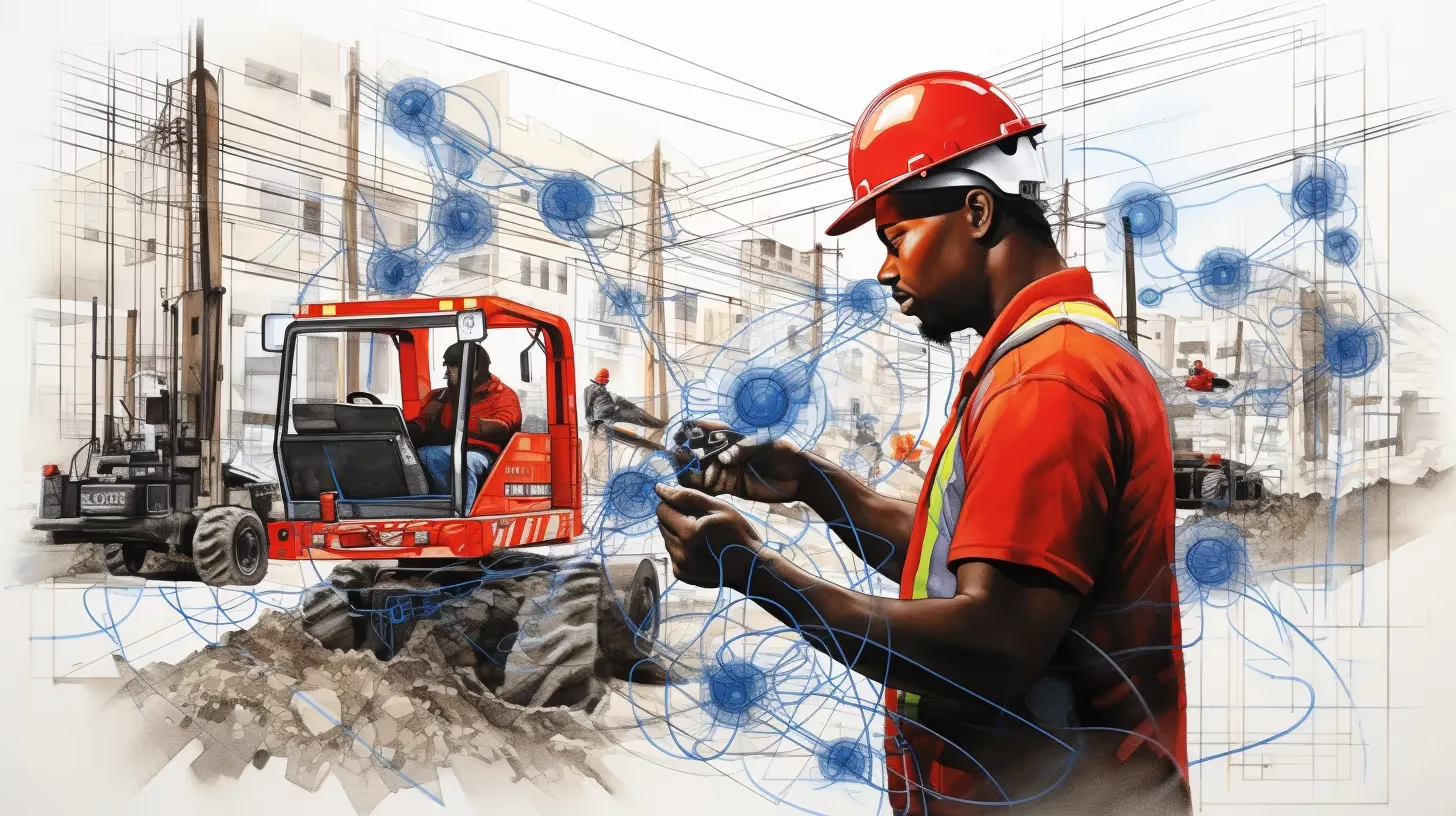
The Significance of Equipment Management in Construction
Effective equipment management is a cornerstone for success in the dynamic construction world, where every project involves an intricate web of tasks, timelines, and resources. This article explores why equipment management is paramount in the construction industry and how it contributes to the seamless execution of projects.
Optimized Resource Allocation
Construction projects are complex endeavors that require coordinating various resources, with equipment being a significant component. Effective equipment management ensures that resources are allocated optimally, with the right equipment assigned to specific tasks. This allocation prevents overburdening certain equipment while underutilizing others, enhancing overall project efficiency.
Minimized Downtime and Delays
Equipment breakdowns can lead to costly project delays. A well-structured equipment management strategy includes regular maintenance and inspection schedules, reducing the risk of unexpected failures. Timely maintenance prolongs the equipment's lifespan and minimizes downtime, allowing projects to stay on track.
Budget Control
In the construction industry, budgets are tight, and costs must be managed carefully. Equipment management plays a crucial role in controlling expenses. Construction companies can make informed decisions to optimize spending and avoid unnecessary expenditures by monitoring equipment usage, maintenance costs, and potential replacements.
Enhanced Safety
Safety is a top priority on construction sites. Properly managed equipment reduces the likelihood of accidents caused by faulty machinery. Routine maintenance, thorough inspections, and adherence to safety regulations ensure that equipment remains in safe working condition, protecting workers and the project.
Compliance with Regulations
Construction is subject to numerous regulations and standards to ensure environmental protection, worker safety, and overall quality. Effective equipment management ensures that equipment meets these regulatory requirements. Regular inspections and guideline adherence contribute to compliance, preventing legal issues and costly penalties.
Efficiency in Operations
Well-maintained equipment performs optimally, allowing tasks to be completed efficiently. Whether earthmoving, lifting heavy loads, or precision tasks, equipment in good condition enhances operational speed and accuracy. This efficiency directly translates into meeting project deadlines and client expectations.
Long-Term Investment Protection
Construction equipment represents a substantial investment. Proper management, including maintenance and scheduled replacements, protects this investment. Maximizing the lifespan of equipment and minimizing premature replacements contribute to a better return on investment over time.
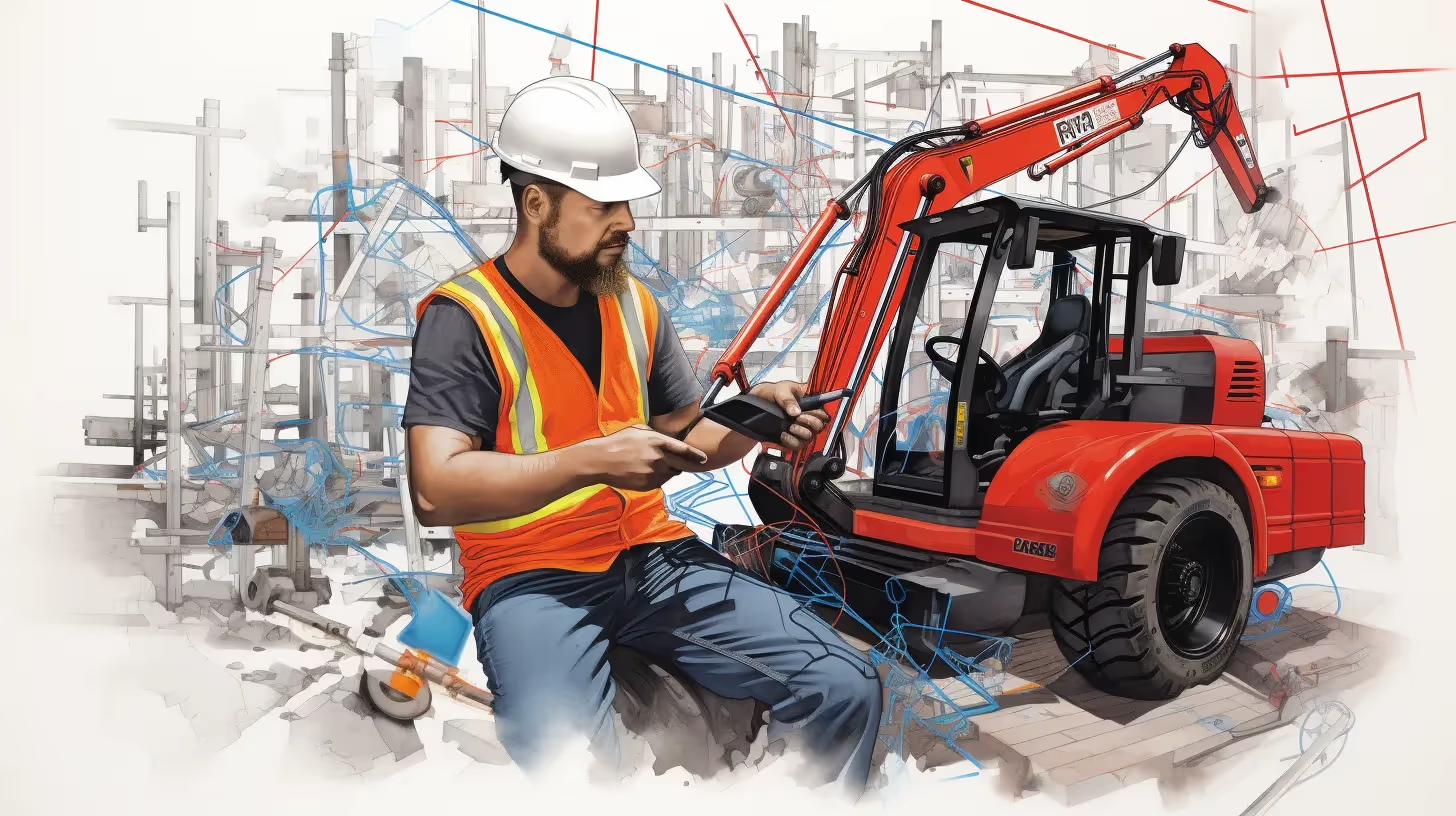
Efficiently Managing Construction Equipment: Strategies and Best Practices
In the dynamic realm of construction, where every task and timeline matters, efficient equipment management becomes a linchpin for success. Construction projects rely heavily on a diverse range of equipment, from heavy machinery to specialized tools. Dive into the strategies and best practices for effectively managing construction equipment, ensuring seamless project execution, and optimal resource utilization.
Centralized Equipment Inventory
A fundamental step in construction equipment management is establishing a centralized inventory. This inventory should detail the company's equipment, including specifications, maintenance history, and location. A digital inventory system enhances accessibility and allows real-time updates, ensuring that equipment data remains accurate and actionable.
Equipment Allocation Planning
Planning equipment allocation is a balancing act that requires foresight and coordination. Construction projects often involve multiple tasks that require various types of equipment. Effective equipment management involves anticipating these needs, scheduling equipment allocations, and ensuring that each piece of equipment is utilized to its maximum potential.
Preventive Maintenance Scheduling
Regular preventive maintenance is essential to prevent unexpected breakdowns and costly downtime. Create a comprehensive maintenance schedule for each piece of equipment, including routine inspections, lubrication, and part replacements. This approach extends equipment lifespan and reduces the chances of interruptions during critical project phases.
Real-Time Equipment Tracking
Utilizing technology for real-time equipment tracking can revolutionize construction equipment management. GPS and RFID technology allows companies to monitor the location and status of equipment, enabling quick retrieval and optimized allocation. This technology also helps prevent equipment theft and aids in recovery if theft does occur.
Training and Skill Development
Efficient equipment management isn't just about the machinery—it's also about the people operating it. Provide comprehensive training to equipment operators, ensuring they understand proper usage, safety protocols, and maintenance procedures. Skilled operators contribute to equipment longevity and safe project execution.
Performance Monitoring and Analytics
Implement data-driven decision-making by utilizing performance monitoring and analytics tools. These tools provide insights into equipment utilization, downtime patterns, maintenance costs, and overall efficiency. By analyzing this data, construction companies can make informed choices to optimize resource allocation and improve processes.
Equipment Retirement and Replacement Strategy
Every piece of equipment has a finite lifespan. Establish a strategy for equipment retirement and replacement based on maintenance costs, efficiency decline, and technological advancements. A well-defined strategy prevents holding onto outdated equipment and allows for timely upgrades.
Vendor Relationship Management
Effective equipment management involves maintaining positive relationships with equipment vendors. Regular communication can lead to favorable terms for maintenance services, spare parts, and equipment upgrades. Strong vendor relationships can also provide access to industry insights and best practices.
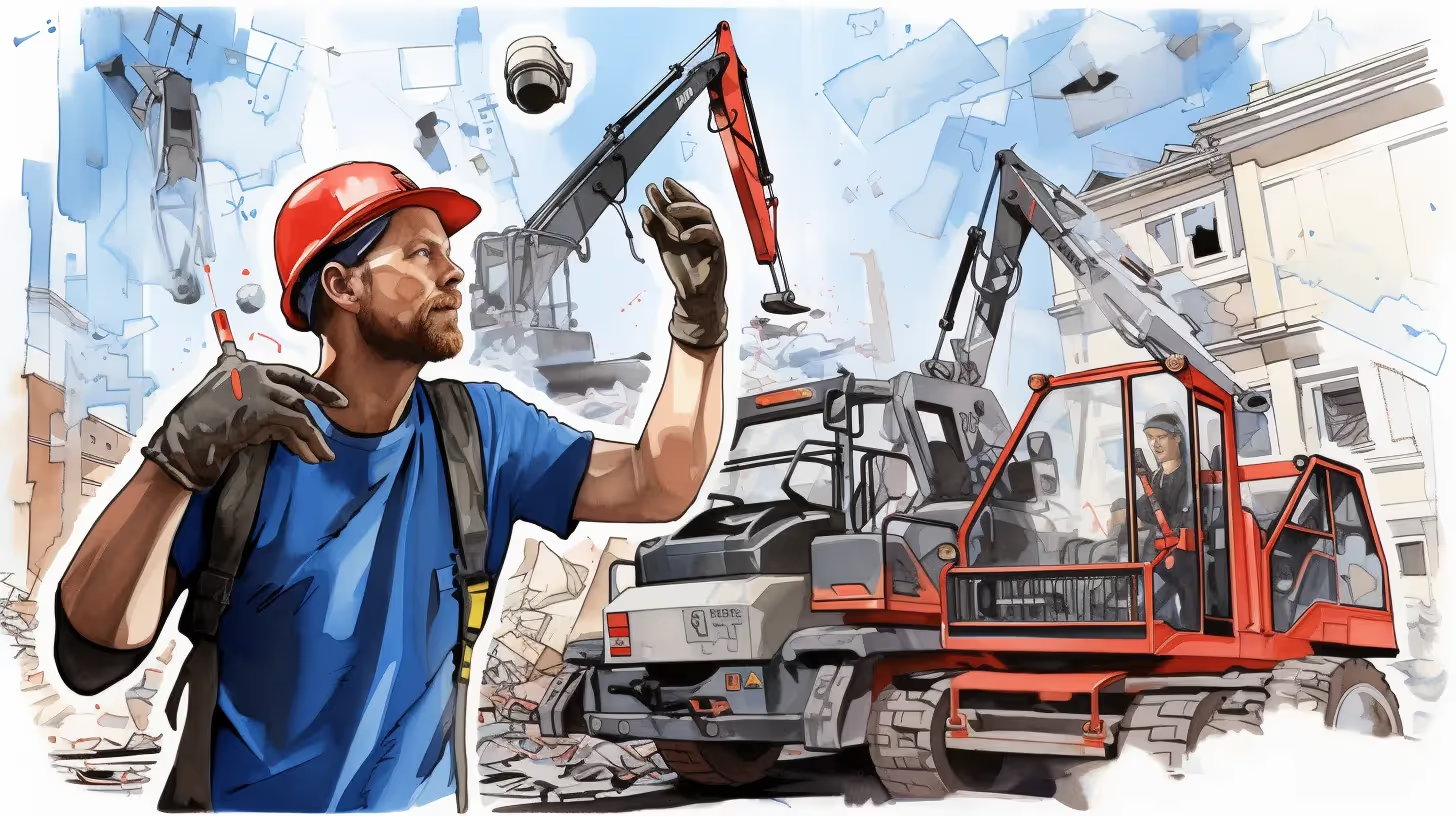
Benefits of Construction Equipment Management Software
In the bustling construction world, where every moment and resource count, harnessing technology is essential for optimal project management. Construction Equipment Management Software (CEMS) has emerged as a game-changer, streamlining operations and enhancing efficiency across the industry. Dive into CEMS's many benefits, empowering construction companies to navigate complex projects precisely and confidently.
Enhanced Equipment Visibility and Tracking
CEMS provides real-time visibility into construction equipment's location, status, and utilization. Through integrated GPS and RFID technology, construction companies can track the movement of equipment across various job sites. This transparency eliminates guesswork, reduces equipment loss, and enables efficient allocation based on actual usage.
Streamlined Maintenance Management
Effective maintenance is the backbone of equipment longevity. CEMS allows construction companies to schedule and track preventive maintenance tasks seamlessly. Automated alerts for maintenance intervals ensure that equipment remains in peak condition, reducing downtime due to unexpected breakdowns and costly repairs.
Data-Driven Decision Making
CEMS generates comprehensive data and analytics on equipment performance, utilization rates, and maintenance costs. This data-driven approach empowers construction companies to make informed decisions about equipment allocation, retirements, and replacements. Optimization of resource allocation leads to cost savings and improved project timelines.
Improved Resource Allocation
Efficient resource allocation is a hallmark of successful construction projects. CEMS optimizes equipment allocation by analyzing project requirements and equipment availability. This prevents underutilization or overloading of equipment, resulting in streamlined operations and enhanced project efficiency.
Reduced Downtime and Delays
Downtime can be a significant roadblock in construction. CEMS minimizes downtime by enabling proactive maintenance and quick response to breakdowns. Timely care ensures that equipment is always ready for use, contributing to uninterrupted project progress and on-time completion.
Compliance and Documentation
Construction projects are subject to regulatory requirements and safety standards. CEMS assists in compliance by generating detailed maintenance records, inspection reports, and safety logs. This documentation keeps construction companies compliant and simplifies audits and inspections.
Cost Control and Budgeting
CEMS empowers construction companies to manage equipment-related expenses effectively. Companies can create accurate budgets and control costs throughout the project lifecycle by monitoring maintenance costs, fuel consumption, and other operational expenses.
Enhanced Equipment Utilization
Underutilized equipment could be a more efficient use of resources. CEMS analyzes equipment utilization patterns and identifies instances of low utilization. This insight allows construction companies to adjust by reallocating equipment or optimizing project schedules.
Scalability and Growth
As construction companies expand their operations, managing equipment becomes more complex. CEMS is scalable, accommodating the growing needs of construction projects. Whether managing a single project or a portfolio of ventures, CEMS adapts to ensure consistent efficiency.
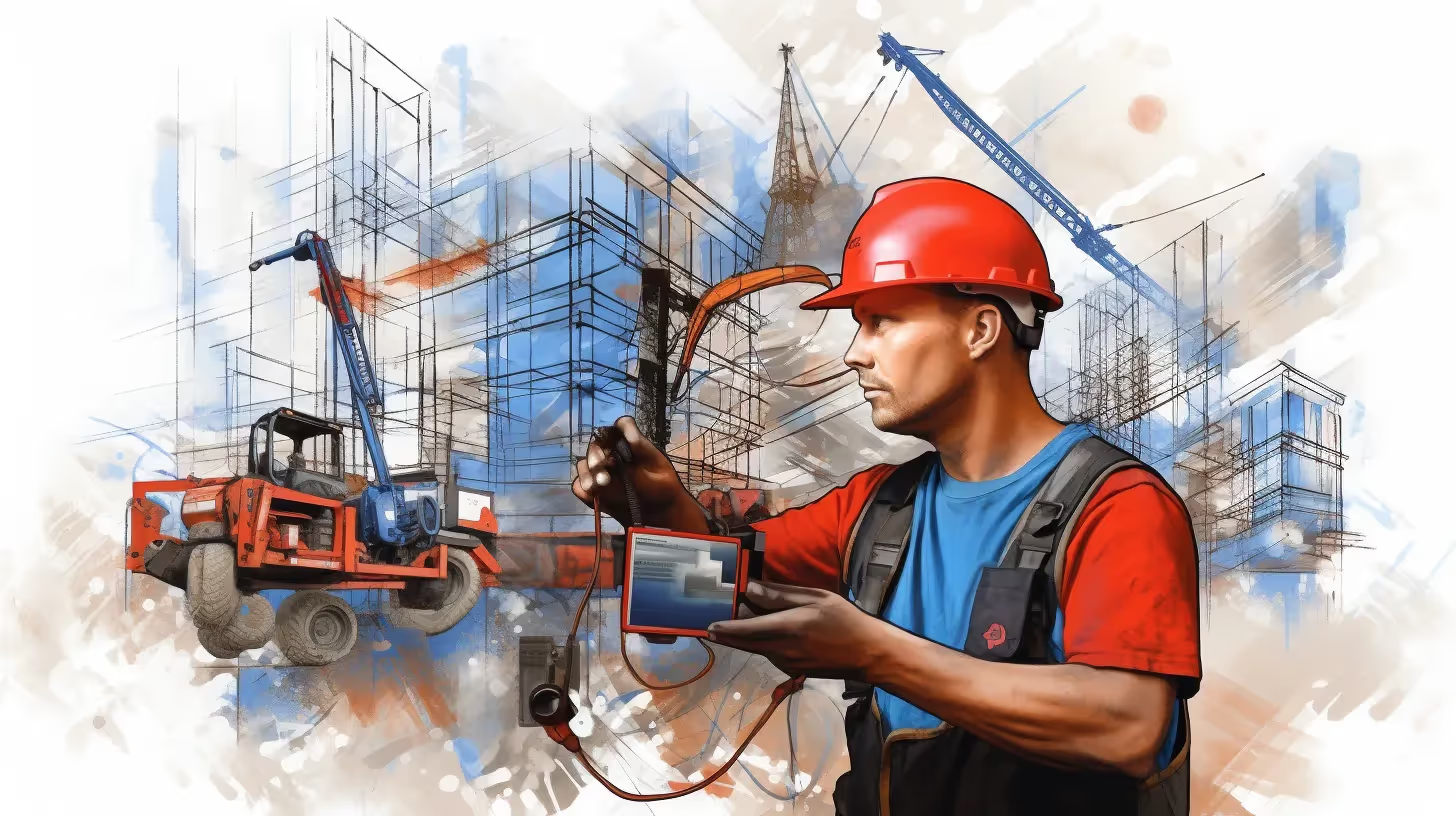
How Construction Equipment Tracking Software Works
Technology revolutionizes project management in the dynamic realm of construction, where precision and coordination are paramount. Construction Equipment Tracking Software (CETS) emerges as a vital tool, offering real-time insights and control over equipment utilization, location, and maintenance. Dive into the inner workings of CETS, showcasing how it enhances project efficiency and streamlines construction operations.
Understanding Construction Equipment Tracking Software
CETS is a comprehensive digital solution integrating cutting-edge technologies to provide construction companies detailed visibility into their equipment fleet. CETS offers real-time tracking, monitoring, and construction equipment management across multiple job sites through GPS, RFID, and cloud-based platforms.
Real-Time Location Tracking
One of the core features of CETS is real-time location tracking. Equipped with GPS technology, each piece of equipment is tagged, allowing construction managers to monitor its exact location on a digital map. This tracking eliminates manual check-ins and enables swift retrieval for urgent tasks.
Utilization Monitoring
CETS goes beyond location tracking by providing insights into equipment utilization. By analyzing data on equipment usage, construction companies can identify patterns of underutilization or overuse. This information enables better allocation of resources and informed decisions on equipment distribution.
Maintenance Scheduling and Alerts
Preventive maintenance is a cornerstone of equipment longevity. CETS automates maintenance scheduling by tracking equipment usage and sending alerts for maintenance tasks. These reminders ensure that equipment remains in peak condition, reducing the risk of breakdowns and unplanned downtime.
Geofencing and Site Management
Geofencing is a powerful feature of CETS that allows construction managers to create virtual boundaries around job sites. When equipment crosses these boundaries, alerts are triggered, providing insights into equipment movement and usage patterns. This feature aids in site management and enhances security.
Customized Reporting
CETS generates customized reports that comprehensively overview equipment performance, utilization rates, and maintenance history. These reports enable data-driven decision-making, allowing construction companies to optimize operations and control costs.
Integration with Maintenance Workflows
CETS seamlessly integrates with maintenance workflows. When a maintenance task is due, the software generates work orders and assigns tasks to relevant personnel. This integration ensures that maintenance activities are executed promptly and efficiently.
Data Security and Accessibility
CETS operates on secure cloud-based platforms, ensuring data integrity and protection. Authorized personnel can access the software from various devices to monitor equipment status and make informed decisions from any location.
Scalability and Adaptability
As construction projects evolve, CETS adapts to changing needs. It accommodates the addition of new equipment, the expansion of job sites, and the growing demands of projects. This scalability ensures that CETS remains a valuable tool throughout a construction company's journey.
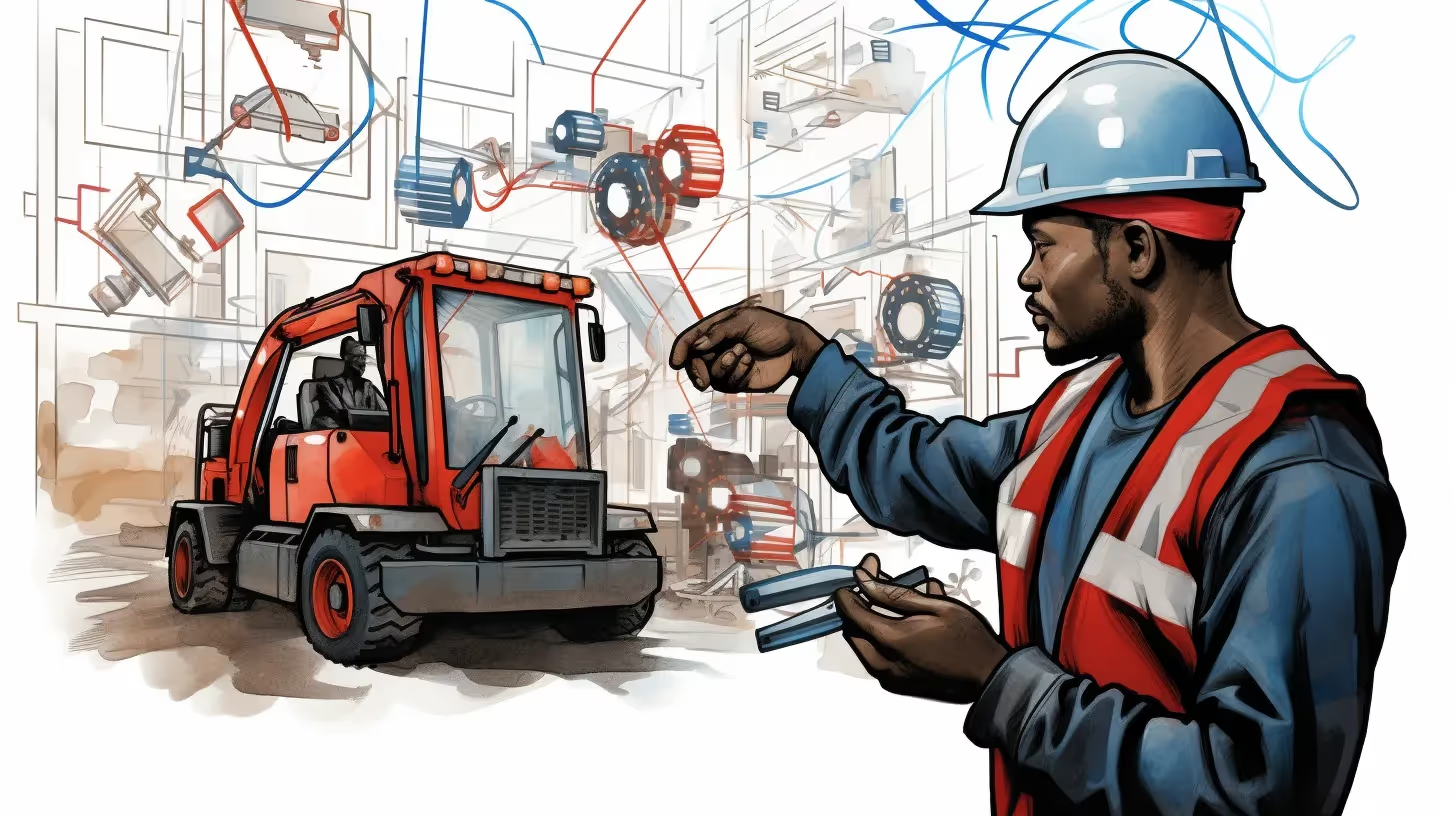
Key Features of Construction Equipment Management Software
In the ever-evolving construction landscape, where precision and efficiency drive success, Construction Equipment Management Software (CEMS) emerges as a crucial asset. The right CEMS can significantly impact project timelines, resource allocation, and operational excellence. Dive into the essential features to look for when selecting CEMS, ensuring that your construction projects are equipped for success.
Real-Time Equipment Tracking
Real-time tracking is the backbone of effective CEMS. This feature employs GPS technology to provide up-to-the-minute location data for each piece of equipment. Real-time tracking eliminates manual check-ins, enhances equipment visibility, and aids in swift retrieval when equipment is needed urgently.
Utilization Insights
A robust CEMS should offer insights into equipment utilization. By analyzing usage patterns, construction managers can identify equipment that is either underutilized or overused. This information enables optimized resource allocation, ensuring that each piece of equipment contributes to project efficiency.
Maintenance Scheduling and Alerts
Preventive maintenance is paramount for equipment longevity. CEMS should facilitate automated maintenance scheduling based on usage data. The software should send alerts for upcoming maintenance tasks, ensuring that equipment remains in optimal condition and reducing the risk of unexpected breakdowns.
Geofencing Capabilities
Geofencing is a valuable feature that allows construction managers to create virtual boundaries around job sites. When equipment enters or exits these boundaries, alerts are triggered. Geofencing enhances site management, aids theft prevention, and provides insights into equipment movement.
Customized Reporting
Detailed reporting is essential for informed decision-making. A comprehensive CEMS should generate customized reports that offer insights into equipment performance, utilization rates, maintenance history, and more. Customizable reports allow construction managers to analyze data relevant to their specific needs.
Integration with Maintenance Workflows
Efficient CEMS should seamlessly integrate with maintenance workflows. When maintenance is due, the software should generate work orders and assign tasks to appropriate personnel. Integration streamlines maintenance processes, ensuring that equipment remains in top condition.
Cloud-Based Accessibility
Cloud-based accessibility ensures authorized personnel can access CEMS data from various devices and locations. This feature enhances collaboration, allowing construction managers to monitor equipment status and make decisions remotely.
Data Security
CEMS deals with sensitive equipment and project data. The software must employ robust security measures to protect this information. Look for features such as encryption, user authentication, and regular security updates.
Scalability
As construction projects evolve, so do equipment needs. A scalable CEMS can accommodate the addition of new equipment and the expansion of project sites. Scalability ensures that the software remains an effective tool as your construction endeavors grow.
User-Friendly Interface
An intuitive user interface is essential for CEMS adoption. The software should be user-friendly, requiring minimal training for personnel to navigate and utilize its features effectively.
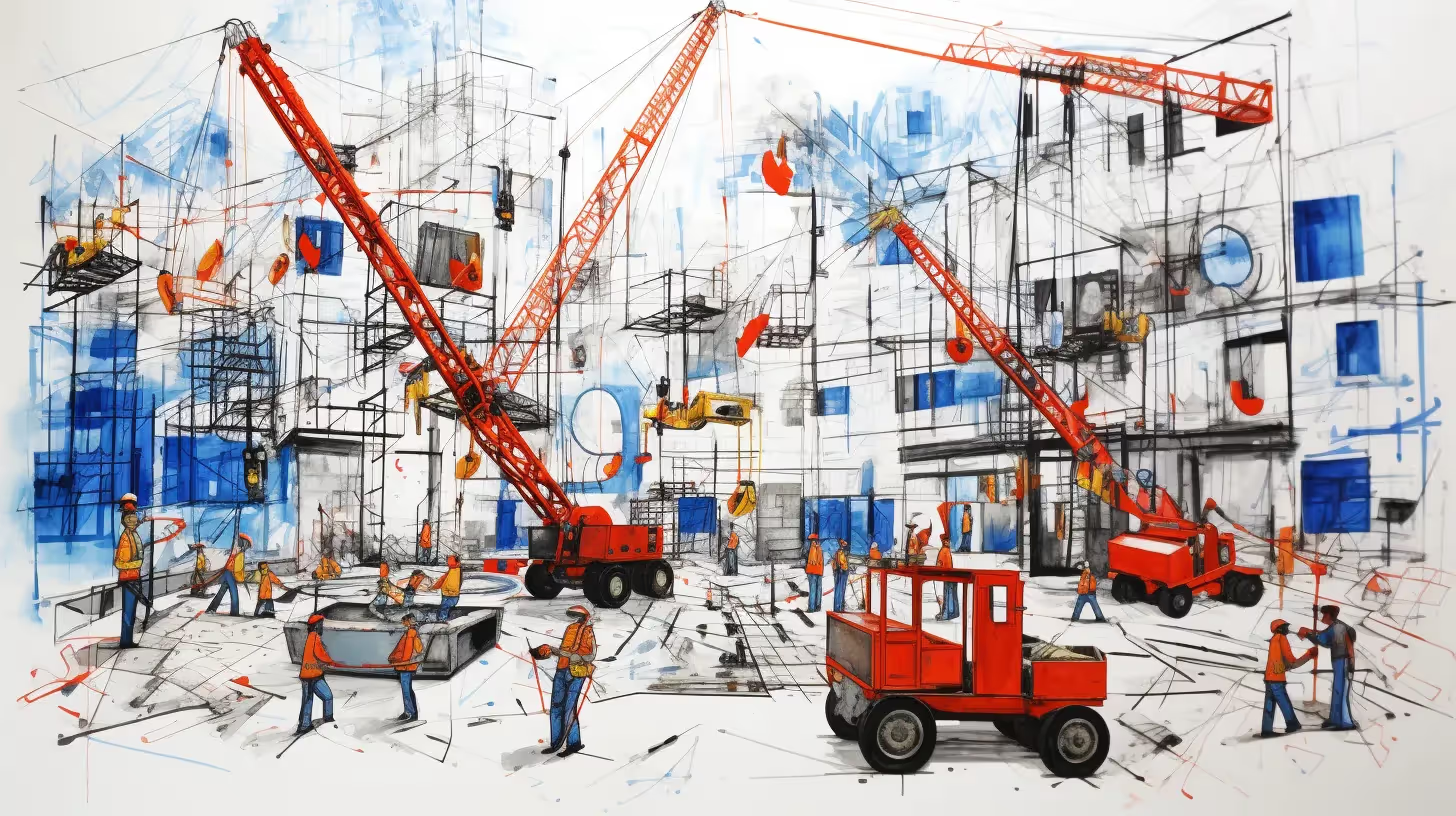
How Construction Equipment Software Improves Operations
In the fast-paced construction world, where time and resources are precious commodities, Construction Equipment Software (CES) emerges as a transformative tool. This software streamlines processes enhances decision-making, and optimizes resource utilization. Dive into how CES improves construction operations, making every moment and resource count.
Real-Time Visibility and Tracking
CES provides real-time visibility into the location and status of construction equipment. Construction companies can track equipment movement across job sites through integrated GPS and RFID technology. This transparency eliminates guesswork, reduces equipment loss, and efficiently allocates equipment.
Streamlined Maintenance Management
Maintenance is essential for equipment longevity. CES simplifies maintenance scheduling by automating reminders and alerts based on usage patterns. This proactive approach reduces unexpected breakdowns, extends equipment lifespan, and minimizes downtime.
Data-Driven Decision Making
CES generates data and analytics on equipment performance, utilization rates, and maintenance costs. This data-driven approach empowers construction managers to make informed decisions. Optimization of equipment allocation based on data leads to cost savings and streamlined operations.
Efficient Resource Allocation
CES analyzes project requirements and equipment availability to optimize resource allocation. By ensuring the right equipment is in the right place at the right time, construction companies enhance operational efficiency and avoid delays caused by equipment unavailability.
Reduced Downtime and Delays
Unplanned equipment downtime can derail construction projects. CES minimizes downtime by facilitating proactive maintenance and quick response to breakdowns. This ensures that equipment is ready for use, contributing to uninterrupted project progress.
Compliance and Documentation
Construction projects are subject to regulations and safety standards. CES generates detailed maintenance records, inspection reports, and safety logs. This documentation keeps construction companies compliant and simplifies audits and inspections.
Cost Control and Budgeting
CES monitors maintenance costs, fuel consumption, and operational expenses. This data enables construction managers to create accurate budgets and control costs throughout the project lifecycle. Efficient resource allocation leads to cost savings.
Enhanced Equipment Utilization
Equipment underutilization is wasteful. CES analyzes equipment usage patterns and highlights underutilized assets. By optimizing equipment deployment, construction companies can ensure that resources are maximized.
Scalability and Adaptability
As construction companies grow, CES scales to accommodate new equipment and projects. This adaptability ensures that the software remains a valuable asset as operations expand.
Conclusion
Construction Equipment Software reshapes the landscape of construction operations. By providing real-time visibility, streamlining maintenance, facilitating data-driven decisions, optimizing resource allocation, and ensuring compliance, CES empowers construction companies to navigate complexities with precision. Through the adoption of CES, construction operations are positioned for success, achieving efficiency and excellence in every project.
Explore the transformative solutions UCS Logistics offers to enhance your construction equipment management. Visit our services page to discover how we can contribute to your construction projects.
Takeaways from the Article:
Importance of Technology in Construction
In the ever-evolving world of construction, leveraging technology, especially Construction Equipment Software (CES), is vital for efficiency and successful project outcomes.
Real-Time Equipment Visibility
CES offers real-time tracking of equipment, integrated with GPS and RFID technology, providing construction companies with accurate location data and insights into equipment availability.
Maintenance Management Simplified
CES automates maintenance schedules, sending alerts for upcoming tasks, ensuring equipment remains in optimal working condition and reducing unplanned downtime.
Data-Driven Decision Making
Comprehensive data and analytics generated by CES empower construction managers to make informed decisions regarding equipment allocation, usage patterns, and maintenance schedules.
Enhanced Resource Allocation
CES optimizes resource allocation by analyzing project requirements and equipment availability, ensuring the right equipment is allocated to the right tasks.
Minimized Downtime and Delays
CES minimizes equipment downtime by enabling proactive maintenance and quick response to breakdowns, ensuring uninterrupted project progress.
Compliance and Documentation
CES aids in regulatory compliance by generating detailed maintenance records, inspection reports, and safety logs.
Cost Control and Budgeting
Monitoring of maintenance costs, fuel consumption, and operational expenses by CES allows construction managers to create accurate budgets and control costs.
Enhanced Equipment Utilization
CES analyzes equipment usage patterns, identifying underutilized assets, allowing for more effective equipment allocation.
Scalability and Adaptability
CES adapts to the changing needs of construction projects, accommodating the addition of new equipment and the expansion of job sites.
Reminder of the Post’s Main Point
Construction Equipment Software (CES) plays a pivotal role in optimizing construction operations by offering real-time equipment visibility, streamlined maintenance management, data-driven decision-making, and efficient resource allocation, leading to successful project outcomes.