Reverse logistics, encompassing product returns, recycling, and the flow of goods from consumers back to manufacturers or retailers, presents a complex landscape filled with challenges. This article will explore the common reverse logistics challenges businesses face and how they intersect with various critical aspects, including supply chain efficiency, customer returns, sustainability, inventory management, cost-efficiency, environmental impact, technology solutions, customer satisfaction, regulatory compliance, and financial implications.
The Multifaceted Challenges of Reverse Logistics
Reverse logistics involves a diverse set of challenges that impact different facets of a business:
Supply Chain Efficiency
Challenge: Reverse logistics can disrupt the flow of goods in the supply chain, affecting operational efficiency.
Solution: Implement technology-driven tracking and visibility solutions to optimize the reverse supply chain.
Customer Returns
Challenge: Handling customer returns efficiently and maintaining high customer satisfaction can be challenging.
Solution: Employ technology for automated returns processing and clear return policies to enhance customer experience.
Sustainability
Challenge: Ensuring responsible recycling and minimizing environmental impact is vital in reverse logistics.
Solution: Embrace sustainable practices, including eco-friendly packaging and responsible disposal.
Inventory Management
Challenge: Inefficient inventory management of returned items can result in overstocking or waste.
Solution: Utilize technology-driven inventory systems to optimize asset disposition and reduce waste.
Cost-Efficiency
Challenge: Inefficient reverse logistics processes can lead to increased costs.
Solution: Streamline processes using technology solutions to minimize operational costs.
Environmental Impact
Challenge: Ineffective disposal of returned items can contribute to pollution and waste.
Solution: Prioritize responsible recycling and sustainable disposal practices.
Technology Solutions
Challenge: Implementing the right technology can be challenging but is essential for efficient reverse logistics.
Solution: Leverage data analytics, automation, and tracking tools for improved operations.
Customer Satisfaction
Challenge: Handling returns efficiently and communicating effectively with customers is critical for satisfaction.
Solution: Utilize technology for transparent communication and streamlined returns processing.
Regulatory Compliance
Challenge: Different industries may be subject to strict product returns and disposal regulations.
Solution: Ensure adherence to regulations through technology-driven compliance monitoring.
Financial Implications
Challenge: Inefficient reverse logistics can have financial repercussions, including increased costs and missed sales opportunities.
Solution: Optimize processes for cost savings and improved financial outcomes.
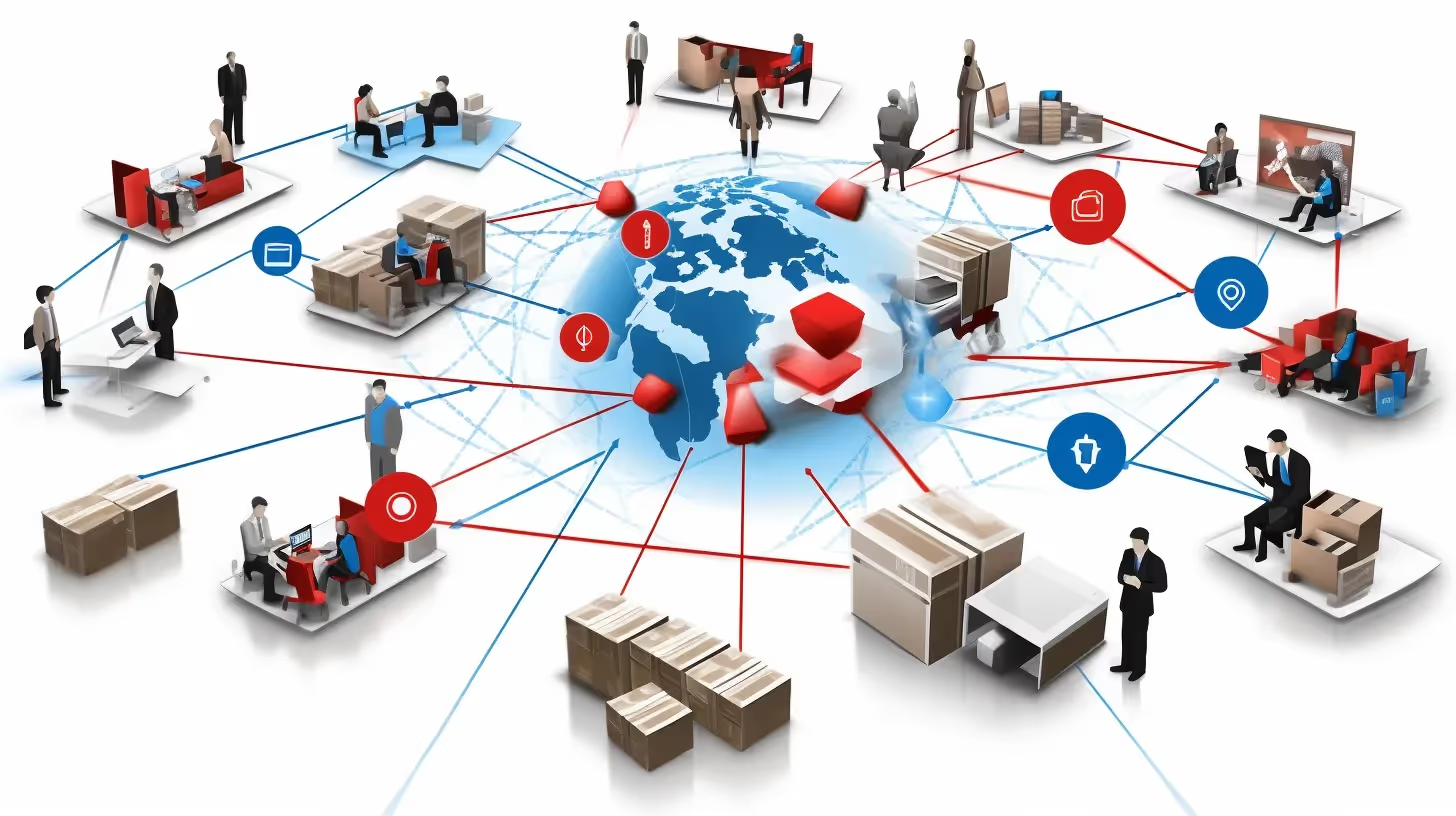
Understanding Reverse Logistics: Why It Matters
Reverse logistics is a critical aspect of modern supply chain management that deals with the flow of products or materials from the end consumer to the manufacturer or retailer. While traditional logistics focuses on getting products from the manufacturer to the consumer, reverse logistics manages the return, recycling, remanufacturing, and disposal of products. In this article, we will delve into reverse logistics, why it is important, and how it impacts various aspects of business, including customer satisfaction, environmental concerns, and financial implications.
What is Reverse Logistics?
Reverse logistics, often called "RL," moves goods from their final destination to the manufacturer or a designated return center. This process encompasses various activities, such as product returns, recycling, warranty recovery, and disposal of defective or obsolete items.
Reverse logistics differs significantly from forward logistics, which focuses on the efficient movement of goods from manufacturers to consumers. In reverse logistics, the flow of goods is in the opposite direction, involving returns, recalls, and the recovery of valuable materials.
Why is Reverse Logistics Important?
Reverse logistics plays a pivotal role in today's business landscape for several reasons:
Customer Satisfaction
Customer returns and exchanges are common occurrences in retail and e-commerce. Efficient reverse logistics processes are essential to ensure a seamless and satisfactory customer experience. When returns are handled promptly and efficiently, customers are more likely to trust the brand and make future purchases.
Sustainability
In an era of increasing environmental awareness, businesses are pressured to adopt sustainable practices. Reverse logistics is a key component of sustainability efforts as it enables product recycling and responsible disposal. Sustainable practices in reverse logistics can help reduce the environmental impact of businesses.
Inventory Management
Managing returned items and excess inventory is a challenge that businesses face regularly. Effective reverse logistics processes help identify reusable items, refurbish them, and return them to stock, thus optimizing inventory management and reducing waste.
Cost-Efficiency
Inefficient reverse logistics can increase costs due to mishandled returns, transportation, and storage of returned items. A well-organized reverse logistics system can minimize these costs and improve cost efficiency.
Environmental Impact
Reverse logistics can have a significant environmental impact if not managed properly. Businesses need to address issues related to recycling, waste reduction, and the responsible disposal of products to minimize their environmental footprint.
Technology Solutions
Technology plays a crucial role in streamlining reverse logistics operations. Advanced software, tracking systems, and data analytics can help businesses optimize their processes, reduce errors, and enhance visibility into the reverse supply chain.
Regulatory Compliance
Many industries are subject to strict product returns, recalls, and disposal regulations. Compliance with these regulations is essential to avoid legal issues and maintain a positive brand reputation.
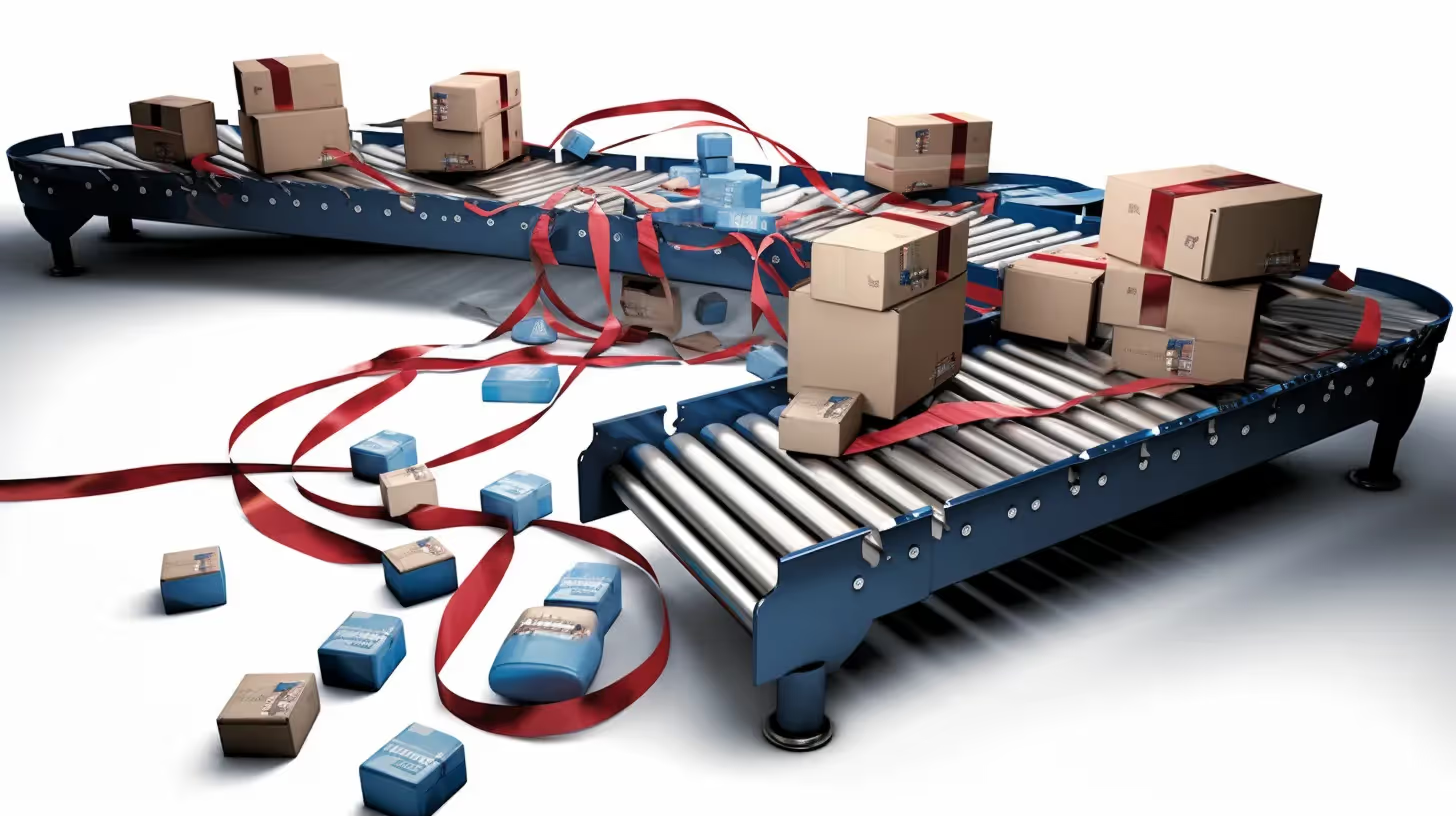
Common Challenges in Reverse Logistics: Navigating the Complex Terrain
Reverse logistics, the intricate process of handling product returns, recycling, and moving goods from the end consumer back to the manufacturer or retailer, presents various challenges that businesses must address. In this article, we'll explore some of the most common challenges faced in reverse logistics and how they impact businesses, including issues related to customer returns, sustainability, inventory management, cost-efficiency, environmental concerns, and the use of technology solutions.
The Complex Landscape of Reverse Logistics
Reverse logistics is often regarded as the "back end" of the supply chain, and its challenges can be just as daunting as those faced in the forward logistics process. Here are some of the key challenges:
Customer Returns
Customer returns are integral to retail and e-commerce but can be complex to manage. Businesses must efficiently process returns, determine the condition of returned items, and decide whether they can be restocked, refurbished, or should be disposed of. Handling returns with care is crucial to maintaining customer satisfaction.
Sustainability
Sustainability is a growing concern in reverse logistics. Businesses must develop sustainable practices to reduce waste, recycle materials, and responsibly dispose of products. Implementing eco-friendly initiatives benefits the environment and enhances a company's reputation.
Inventory Management
Managing returned items and excess inventory poses a significant challenge. It's essential to have processes to identify reusable items, repair or refurbish them and return them to stock. Efficient inventory management in reverse logistics can help reduce waste and cut costs.
Cost-Efficiency
Inefficient reverse logistics processes can lead to increased costs. Mishandled returns, transportation, and storage of returned items can all contribute to financial challenges. Streamlining reverse logistics operations is crucial for maintaining cost efficiency.
Environmental Impact
Improperly managed reverse logistics can have a negative environmental impact. Products that end up in landfills contribute to pollution and waste. To mitigate these effects, businesses must focus on responsible recycling and disposal practices.
Technology Solutions
Technology plays a pivotal role in addressing reverse logistics challenges. Advanced software, tracking systems, and data analytics can help streamline processes, improve visibility into the reverse supply chain, and reduce errors.
Customer Satisfaction
The way a company handles returns directly affects customer satisfaction. Long wait times for refunds or replacements, unclear return policies, and damaged returns can all lead to dissatisfied customers.
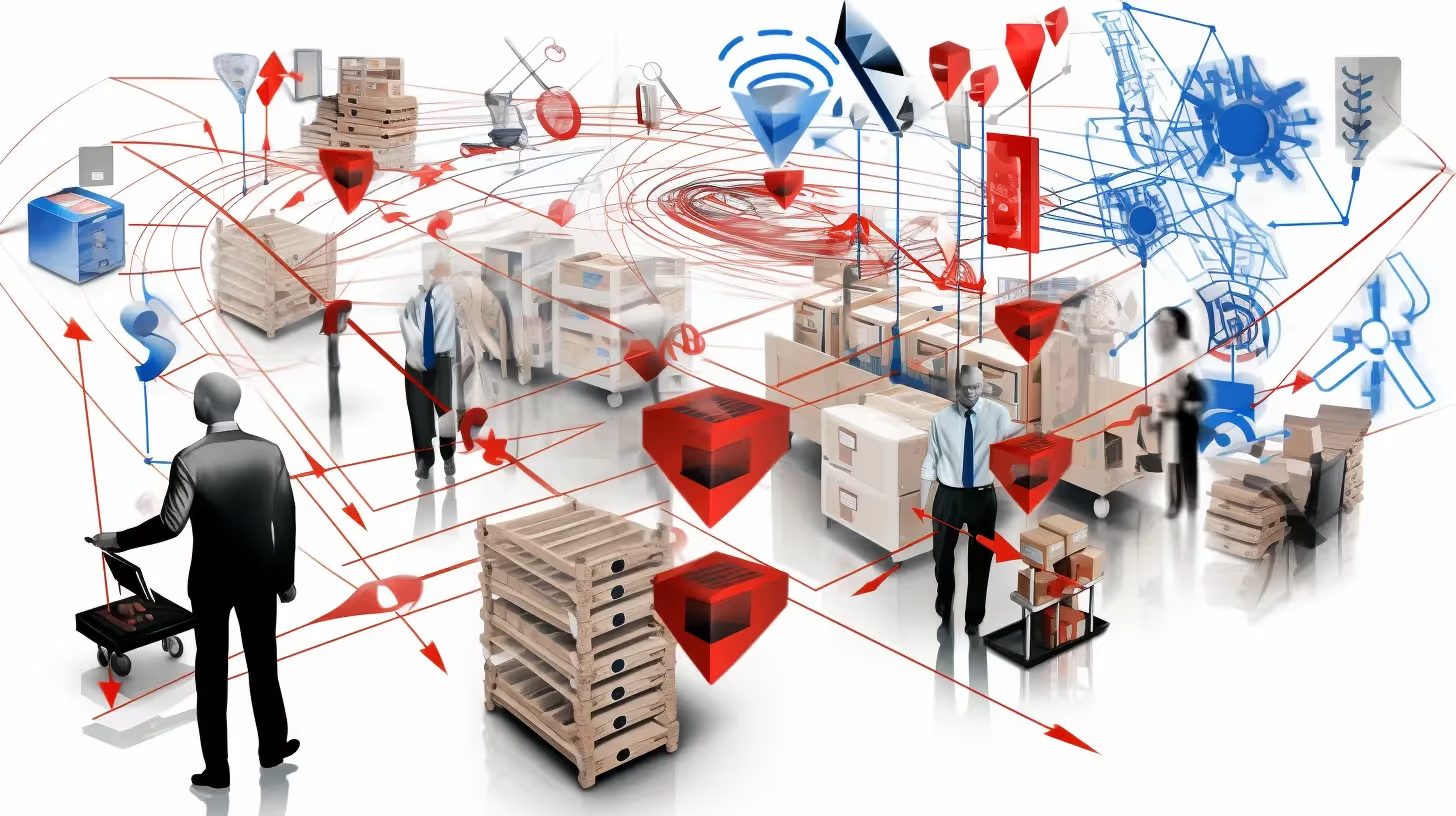
The Impact of Reverse Logistics on Customer Satisfaction
Reverse logistics, managing product returns, recycling, and the movement of goods back from the end consumer to the manufacturer or retailer profoundly impact customer satisfaction. In this article, we'll explore how reverse logistics practices directly influence customer satisfaction and why it's crucial for businesses to excel in this aspect.
The Customer-Centric World of Retail
In today's customer-centric world, where the shopping experience is as important as the product, customer satisfaction is the key to business success. Reverse logistics plays a pivotal role in shaping this satisfaction for several reasons:
Efficient Returns Handling
One of the primary facets of reverse logistics is handling customer returns. How a company manages returns can significantly impact customer satisfaction. Customers appreciate hassle-free, prompt return processes. When returns are processed smoothly, customers are more likely to trust the brand and make future purchases.
Clear Return Policies
Transparent and well-communicated return policies are essential for customer satisfaction. Customers need to know what to expect when returning a product. Unclear or restrictive policies can lead to frustration and dissatisfaction.
Product Condition Assessment
Reverse logistics involves assessing the condition of returned items. Customers expect fair evaluations and refunds or exchanges based on the product's condition. Failing to meet these expectations can result in negative reviews and diminished trust in the brand.
Responsiveness to Customer Inquiries
Customers may have questions or concerns about their returns. A responsive customer support team that can address these inquiries promptly and effectively contributes to overall satisfaction.
Preventing Damaged Returns
Proper packaging and handling during returns are crucial to prevent damage to products. When items arrive in poor condition due to mishandling, it can lead to dissatisfaction and a loss of trust in the company's shipping and return processes.
The Bottom Line: Customer Loyalty
Ultimately, how a business handles reverse logistics directly impacts customer loyalty and repeat business. A satisfied customer is more likely to become a loyal customer who continues to purchase from the company and recommends it to others.
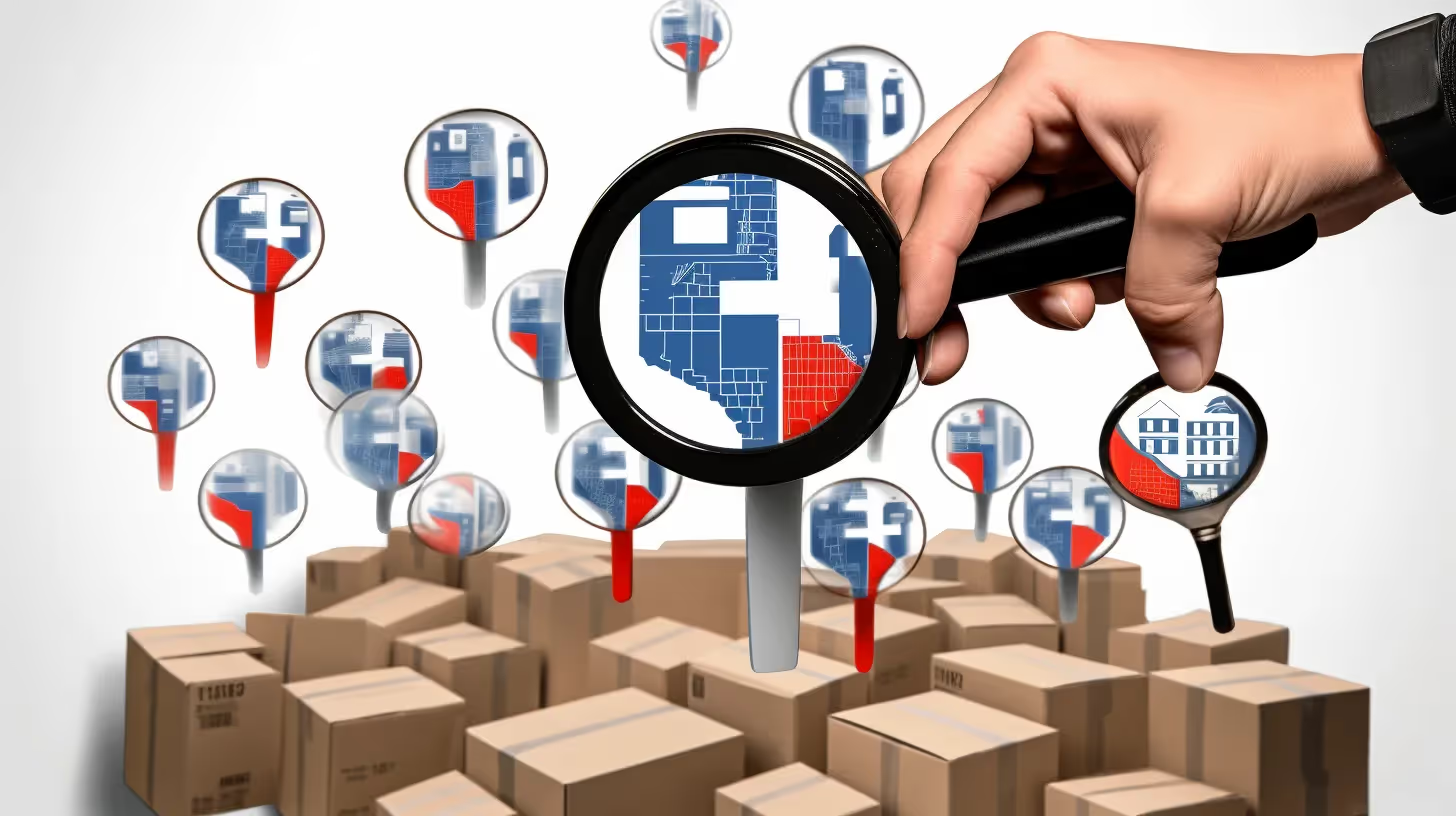
Environmental Concerns in Reverse Logistics: A Sustainable Approach
Reverse logistics, managing product returns, recycling, and the movement of goods back from consumers to manufacturers or retailers is about more than just handling returns efficiently. It also has significant environmental implications. In this article, we'll explore the environmental concerns of reverse logistics and how businesses can adopt sustainable practices to mitigate them.
The Environmental Impact of Reverse Logistics
Reverse logistics has a considerable environmental footprint due to the following factors:
Product Disposal
One of reverse logistics's most pressing environmental concerns is disposing of returned or unsellable products. When items end up in landfills, they contribute to pollution and waste. Companies must seek alternative methods, such as recycling or repurposing, to minimize this impact.
Transportation Emissions
Transporting returned products to the manufacturer or designated return centers can increase carbon emissions. Businesses must optimize transportation routes and consider greener options to reduce their carbon footprint.
Packaging Waste
Returns often involve the use of additional packaging materials. This can lead to excessive waste, as much of this packaging is discarded after a single use. Sustainable packaging practices are crucial to reduce this environmental concern.
Energy Consumption
Reverse logistics operations, such as refurbishing or remanufacturing, require energy. Reducing energy consumption and incorporating renewable energy sources can help mitigate the environmental impact.
E-Waste
In the case of IT asset management, electronic waste (e-waste) is a significant concern. Discarded electronic devices can contain hazardous materials, making proper disposal and recycling imperative for environmental protection.
Adopting Sustainable Practices in Reverse Logistics
To address these environmental concerns, businesses can implement sustainable practices in their reverse logistics processes:
Responsible Recycling
Develop recycling programs to ensure that returned products are properly recycled, especially in the case of electronic devices. This reduces waste and prevents harmful materials from contaminating the environment.
Eco-Friendly Packaging
Use sustainable and biodegradable packaging materials to minimize packaging waste. Encourage customers to reuse or recycle packaging when returning products.
Energy Efficiency
Adopt energy-efficient processes in refurbishing, remanufacturing, and handling returned products. Implement energy management systems to reduce consumption and greenhouse gas emissions.
Transportation Optimization
Streamline transportation routes to minimize emissions and fuel consumption. Consider using electric or hybrid vehicles for transportation when feasible.
Product Design
Design products with sustainability in mind, making them easier to disassemble, refurbish, or recycle. This can reduce the environmental impact during the reverse logistics process.
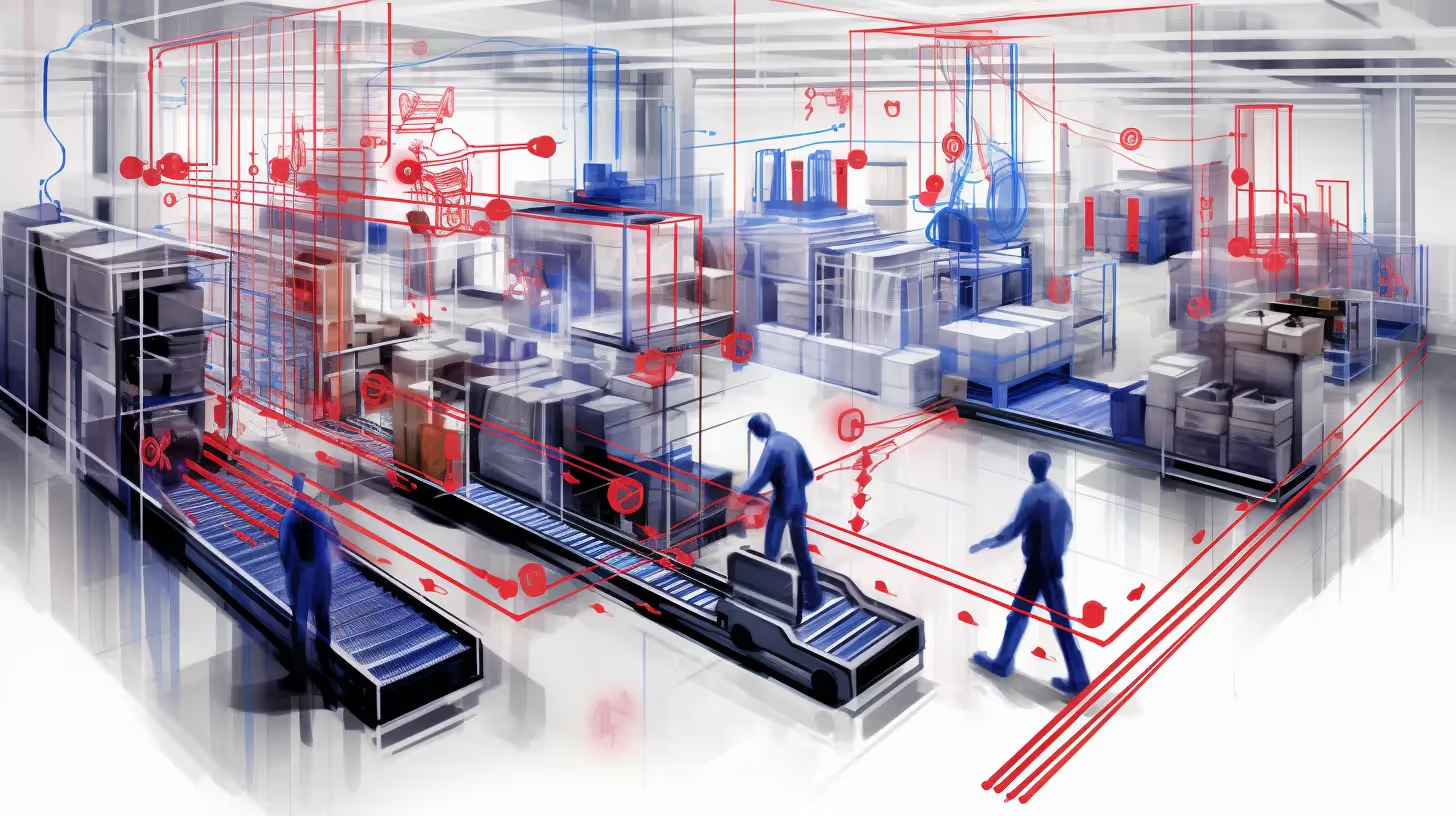
Leveraging Technology for Efficient Reverse Logistics Operations
Reverse logistics, the intricate process of managing product returns, recycling, and the movement of goods from consumers back to manufacturers or retailers, is not immune to the transformative power of technology. This article will explore how technology solutions can enhance and streamline reverse logistics operations, making them more efficient and effective.
The Role of Technology in Reverse Logistics
In recent years, technology has played a pivotal role in addressing the challenges associated with reverse logistics. Here are several ways technology is making a difference:
Data Analytics
Data analytics is a game-changer in reverse logistics. Advanced analytics tools can provide valuable insights into return patterns, product conditions, and reasons for returns. This data helps businesses make informed decisions, reduce return rates, and optimize reverse logistics processes.
Inventory Management Systems
Efficient inventory management is crucial in reverse logistics. Technology-driven inventory systems can track returned products, assess their condition, and determine whether they can be refurbished, restocked, or need disposal. This prevents overstocking, reduces waste, and improves cost efficiency.
Tracking and Visibility
Technology solutions, such as RFID (Radio-Frequency Identification) and GPS tracking, provide real-time visibility into the location and status of returned items. This transparency helps businesses monitor the movement of products and identify potential bottlenecks in the reverse supply chain.
Automation
Automation technologies, including robotic systems and conveyor belts, can expedite processing of returned items. Automated sorting and inspection systems can assess product conditions quickly, allowing for faster decisions on their disposition.
Customer Communication
Technology enables better communication with customers throughout the return process. Automated email notifications, tracking updates, and online return portals enhance the customer experience by providing transparency and convenience.
Sustainable Practices
Technology also supports sustainability efforts in reverse logistics. Recycling and waste reduction programs can be managed more efficiently through digital platforms, ensuring that returned products are responsibly disposed of or repurposed.
The Benefits of Technology in Reverse Logistics
Leveraging technology in reverse logistics brings several benefits:
- Efficiency: Technology streamlines processes, reduces manual errors, and speeds up decision-making, resulting in more efficient operations.
- Cost Savings: Automation and data-driven decision-making help reduce operational costs, minimize waste, and optimize inventory, leading to financial savings.
- Customer Satisfaction: Improved communication and quicker processing of returns lead to higher customer satisfaction and increased trust in the brand.
- Sustainability: Technology supports sustainable practices, helping businesses minimize their environmental impact and meet sustainability goals.
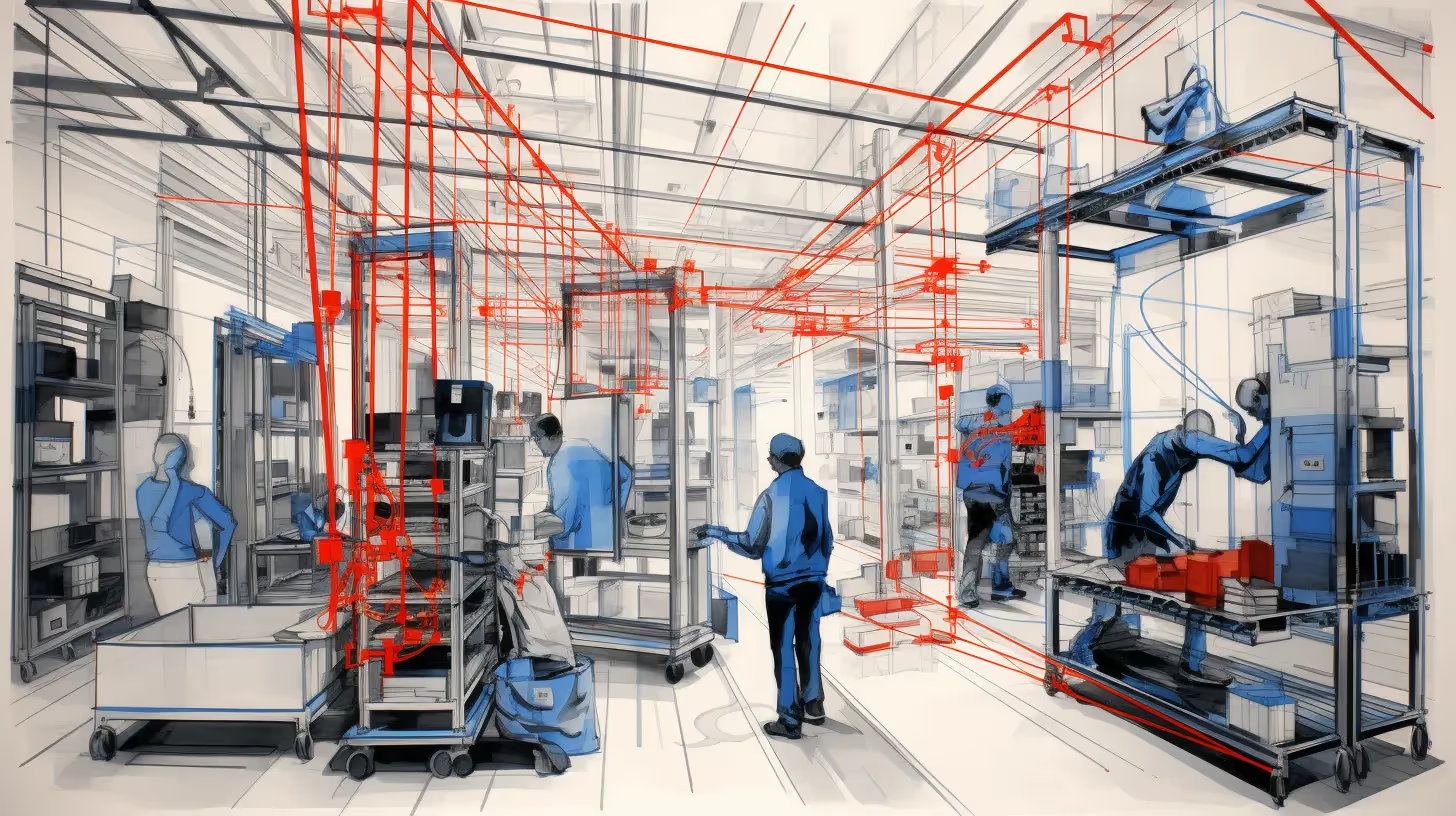
The Financial Implications of Inefficient Reverse Logistics
Reverse logistics, the process of managing product returns, recycling, and the movement of goods from consumers back to manufacturers or retailers, has significant financial implications for businesses. In this article, we'll delve into how inefficient reverse logistics practices can impact a company's bottom line and why optimizing this critical aspect of the supply chain is crucial.
The High Cost of Inefficiency
Inefficient reverse logistics processes can lead to a range of financial challenges for businesses:
Processing Costs
Handling returns, assessing product conditions, and deciding on their disposition involves labor, time, and resources. Inefficient processes can result in higher processing costs due to manual errors, delays, and additional manpower required.
Inventory Management
Please effectively manage returned items to avoid overstocking or underutilization of inventory. Overstocking ties up capital and storage space, while underutilization results in lost revenue opportunities.
Transportation Expenses
Transporting returned products to designated centers can be costly, especially if routes are not optimized or if products are not consolidated efficiently. Excessive transportation costs can eat into profit margins.
Waste and Disposal Costs
Improper disposal of returned or unsellable products can result in waste management expenses. Landfill disposal, in particular, can be costly and environmentally detrimental.
Customer Dissatisfaction
While customer dissatisfaction primarily affects reputation, it can also have direct financial implications. Dissatisfied customers are less likely to make repeat purchases and may share negative experiences, impacting sales and brand image.
Lost Sales Opportunities
Inefficient reverse logistics can lead to delays in restocking or refurbishing returned items. This delay can result in missed sales opportunities as products sit idle or go out of season.
The Financial Benefits of Efficient Reverse Logistics
Conversely, businesses that optimize their reverse logistics operations can reap significant financial benefits:
- Cost Savings: Streamlined processes reduce labor and processing costs, minimizing waste and transportation expenses.
- Improved Inventory Management: Efficient inventory management ensures that returned items are quickly assessed and either refurbished or restocked, maximizing capital utilization.
- Enhanced Customer Satisfaction: Efficient returns processing leads to higher customer satisfaction, increasing the likelihood of repeat business and positive word-of-mouth.
- Reduced Waste Management Costs: Sustainable disposal and recycling practices can reduce waste management expenses.
- Increased Sales Opportunities: Faster restocking or refurbishing of returned items leads to fewer missed sales opportunities.
Conclusion
To navigate these challenges effectively, businesses must adopt a comprehensive approach to reverse logistics. This involves integrating technology solutions, sustainable practices, and streamlined processes into their operations.
By doing so, companies can enhance supply chain efficiency, easily handle customer returns, minimize their environmental footprint, optimize inventory management, reduce costs, improve customer satisfaction, meet regulatory requirements, and achieve better financial outcomes.
At UCS Logistics, we specialize in addressing these common reverse logistics challenges and offer tailored solutions to help businesses thrive in reverse logistics. To learn more about how UCS Logistics can assist your business in navigating these challenges, please visit our website and explore our services. If you have any questions or want to get in touch, don't hesitate to reach out through our contact page.
Takeaways from the Article:
Understanding of Reverse Logistics
Reverse logistics is crucial in modern supply chain management, focusing on the return, recycling, remanufacturing, and disposal of products.
Multifaceted Challenges and Solutions
The article highlights various challenges in reverse logistics, such as supply chain efficiency, customer returns, sustainability, inventory management, cost-efficiency, environmental impact, technology solutions, customer satisfaction, regulatory compliance, and financial implications. For each challenge, a technology-driven or sustainable solution is provided.
Significance of Reverse Logistics
Reverse logistics plays a vital role in customer satisfaction, sustainability, inventory management, cost-efficiency, and environmental impact. Efficient reverse logistics processes can lead to increased customer trust, reduced environmental footprint, optimized inventory, and financial savings.
Role of Technology in Streamlining Operations
Technology, including data analytics, inventory management systems, tracking tools, and automation, plays a pivotal role in enhancing reverse logistics operations. It helps in streamlining processes, reducing errors, improving visibility, and enhancing customer communication.
Financial Implications of Inefficient Practices
Inefficient reverse logistics can lead to increased processing costs, transportation expenses, waste and disposal costs, customer dissatisfaction, and lost sales opportunities. Conversely, efficient practices can result in cost savings, improved inventory management, enhanced customer satisfaction, and increased sales opportunities.
Reminder of the Post’s Main Point
Reverse logistics, which involves the return and recycling of products, presents various challenges for businesses. By understanding these challenges and leveraging technology-driven solutions, businesses can optimize their operations, enhance customer satisfaction, and achieve better financial outcomes.