In asset management, decisions regarding maintenance and upkeep can significantly impact an organization's bottom line and long-term success. It's a critical choice that requires a deep understanding of the costs and benefits of two primary approaches: refurbishment and repair. This article delves into the intricacies of these options, providing valuable insights for top-tier executives, CIOs, IT directors, and asset managers tasked with optimizing asset value, sustainability, and operational efficiency.
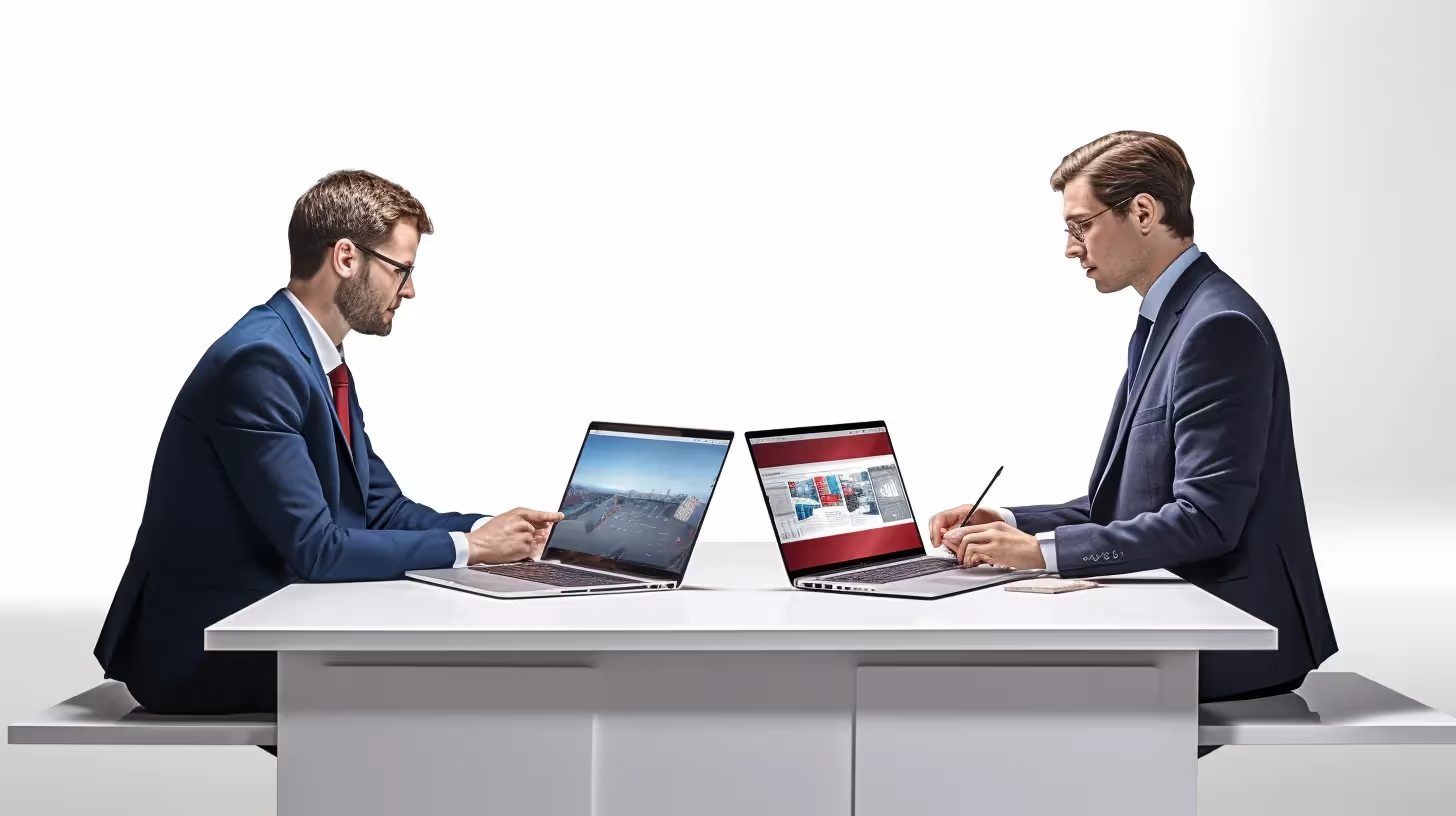
Asset Refurbishment: Breathing New Life into Equipment
Asset refurbishment involves a comprehensive process to rejuvenate equipment to a state that closely resembles its original condition, if not better. This process typically includes:
Inspection and Assessment
Before diving into refurbishment, a thorough assessment is conducted to identify issues and potential areas for improvement. This step is critical in determining the feasibility and cost-effectiveness of refurbishment.
Disassembly
The equipment is disassembled to its core components, allowing for a detailed inspection of individual parts. This step helps in identifying damaged or worn-out segments that need replacement.
Replacement and Upgrade
Defective or outdated components are replaced with new or improved parts. This can include upgrading to the latest technology or ensuring compliance with current industry standards.
Cleaning and Refinishing
The equipment is cleaned meticulously, and any cosmetic imperfections are addressed. Refinishing techniques are employed to enhance the appearance of the asset.
Testing and Quality Assurance
Refurbished equipment undergoes rigorous testing to ensure it functions at optimal levels. This includes performance testing, safety checks, and quality assurance procedures.
Documentation
Detailed records are maintained throughout the refurbishment process, providing transparency and traceability of all actions taken.
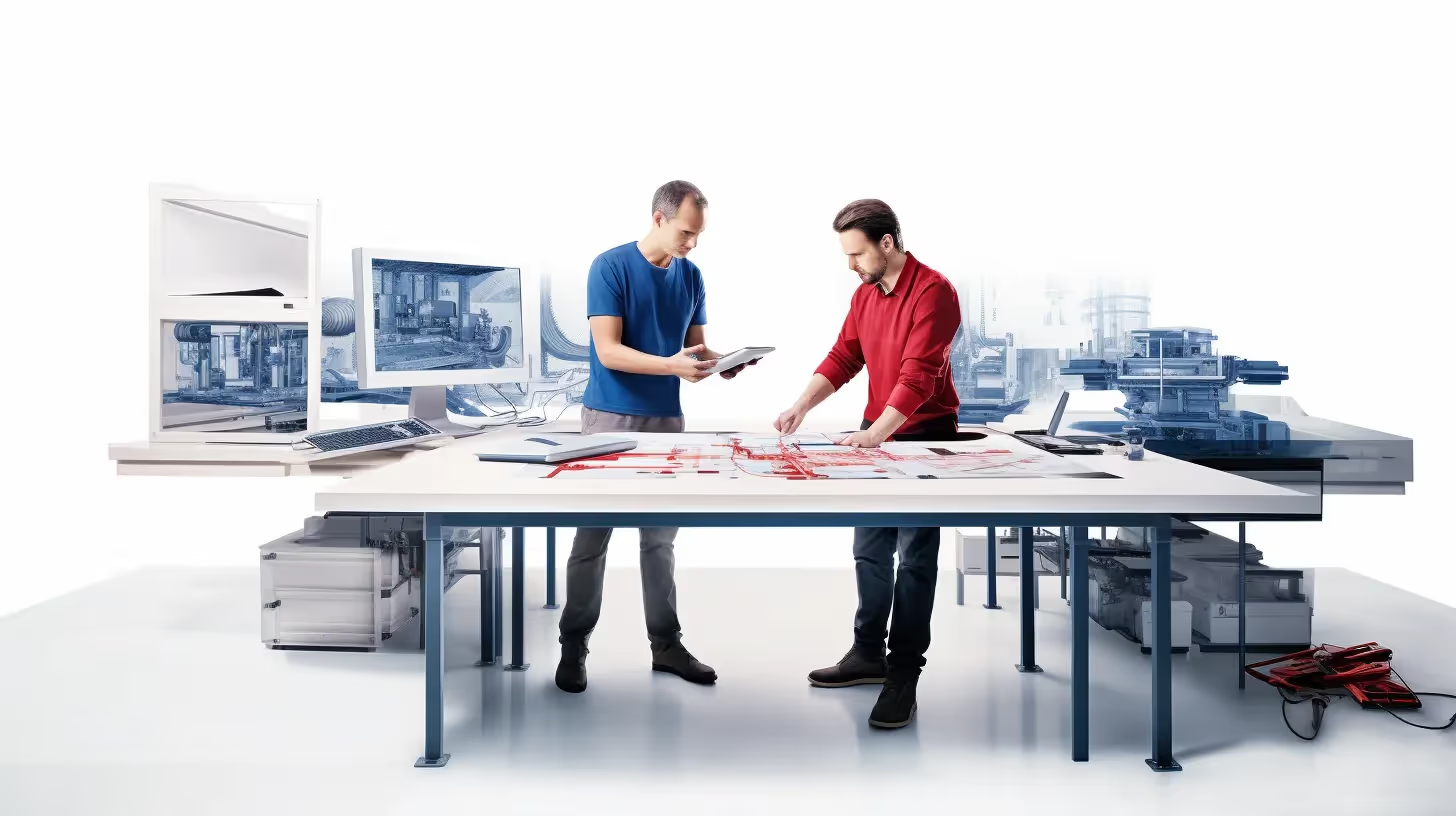
Equipment Repair: Addressing Specific Issues
On the other hand, equipment repair is a focused approach to fixing specific issues or malfunctions within an asset. Here's what typically occurs during equipment repair:
Issue Identification
The equipment is evaluated to pinpoint the exact problem or malfunction. This is a targeted diagnosis to identify the root cause of the issue.
Component Replacement
Only the damaged or faulty components are replaced without a comprehensive overhaul of the entire asset. This minimizes costs and downtime.
Functional Testing
After repair, the equipment undergoes functional testing to ensure that the specific issue has been resolved and it can resume its intended operation.
Minimal Cosmetic Attention
Repair usually does not involve extensive cosmetic work. The focus is on restoring the functionality of the equipment rather than its appearance.
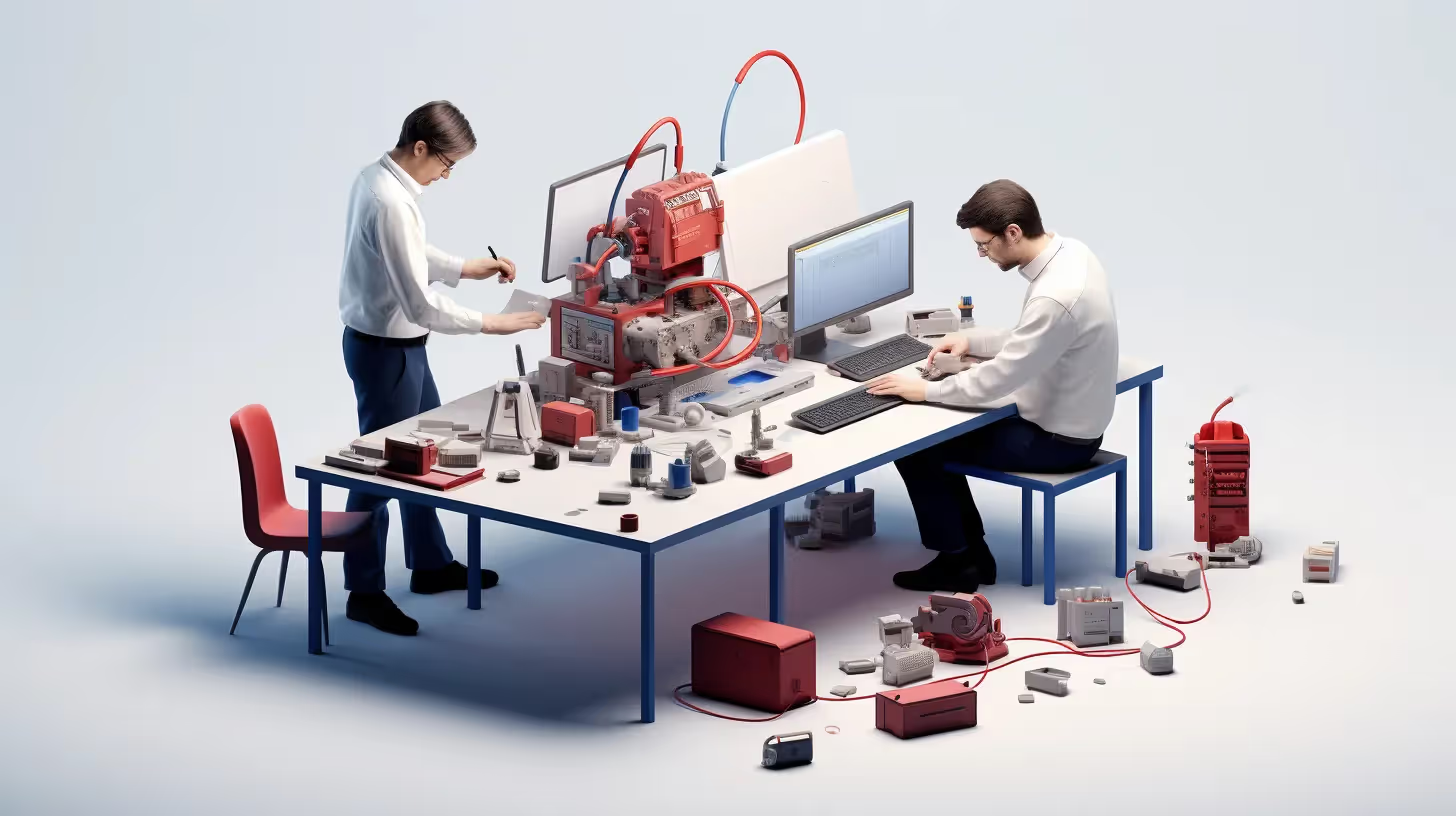
Is Refurbishment Better Than Repair for Long-Term Asset Value?
Maintenance and upkeep decisions in asset management can significantly impact your assets' long-term value. One of the critical questions that often arises is whether refurbishment is a better choice than repair when aiming to preserve and enhance the value of your assets. In this article, we'll explore the nuances of refurbishment and repair, focusing on their implications for long-term asset value.
The Refurbishment Advantage: Maximizing Long-Term Asset Value
Asset refurbishment is a comprehensive process to rejuvenate equipment to a condition that closely resembles or surpasses its original state. Let's delve into the advantages of refurbishment when it comes to long-term asset value:
- Extended Lifespan: Refurbishment involves a thorough assessment and overhaul of the equipment, addressing existing issues and preventing potential problems. This results in a significantly extended lifespan for the asset.
- Performance Optimization: During refurbishment, outdated or subpar components can be replaced with modern, high-performance ones. This upgrade enhances the equipment's capabilities, ensuring it remains competitive and valuable.
- Cost-Effectiveness: Refurbishment may have a higher upfront cost than repair, but it is often more cost-effective in the long run. The reduced need for frequent repairs and delayed asset replacement can lead to substantial savings.
- Environmental Responsibility: Refurbishing assets aligns with sustainability goals by reducing the demand for new resources and minimizing electronic waste. This environmentally responsible approach can enhance your organization's reputation and reduce disposal costs.
- Improved Aesthetics: Refurbishment typically includes cosmetic enhancements, restoring the equipment's appearance to a like-new condition. This can be particularly valuable for assets in customer-facing roles.
The Repair Perspective: A Focused Solution
In contrast, equipment repair is a targeted approach that addresses specific issues or malfunctions within an asset. While it may seem less comprehensive, repair has its merits, especially in certain scenarios:
- Cost Constraints: Repair is generally more budget-friendly than refurbishment. When financial resources are limited, repair can be a practical choice to address immediate issues.
- Minimal Downtime: Repair requires less downtime than the more extensive refurbishment process. Minimizing downtime is a crucial consideration for critical equipment that must remain operational.
- Focused Issue Resolution: When an asset is in overall good condition and only has isolated problems, repair allows for a quick and targeted resolution without needing a full refurbishment.
Making the Decision: Long-Term Value Considerations
The decision between refurbishment and repair should be based on carefully assessing your specific circumstances and long-term asset value objectives. Here are some key considerations to help you make an informed choice:
- Asset Condition: Evaluate the overall condition of the asset. Refurbishment may be the better option to ensure its longevity and performance if it's aging and showing signs of wear and tear.
- Budgetary Constraints: Consider your budget constraints. If finances are limited, repairing specific issues may be a more viable short-term solution, with plans to refurbish or replace the asset.
- Asset Criticality: Assess how critical the asset is to your operations. A swift repair might be the priority for mission-critical equipment where downtime is costly, followed by a more comprehensive refurbishment during planned maintenance windows.
- Sustainability Goals: If sustainability is a key organizational objective, refurbishment aligns better with reducing environmental impact and extending the life of assets.
- Performance Expectations: Determine your performance expectations for the asset. If you require modern capabilities and enhanced performance, refurbishment may be the path to achieving those objectives.
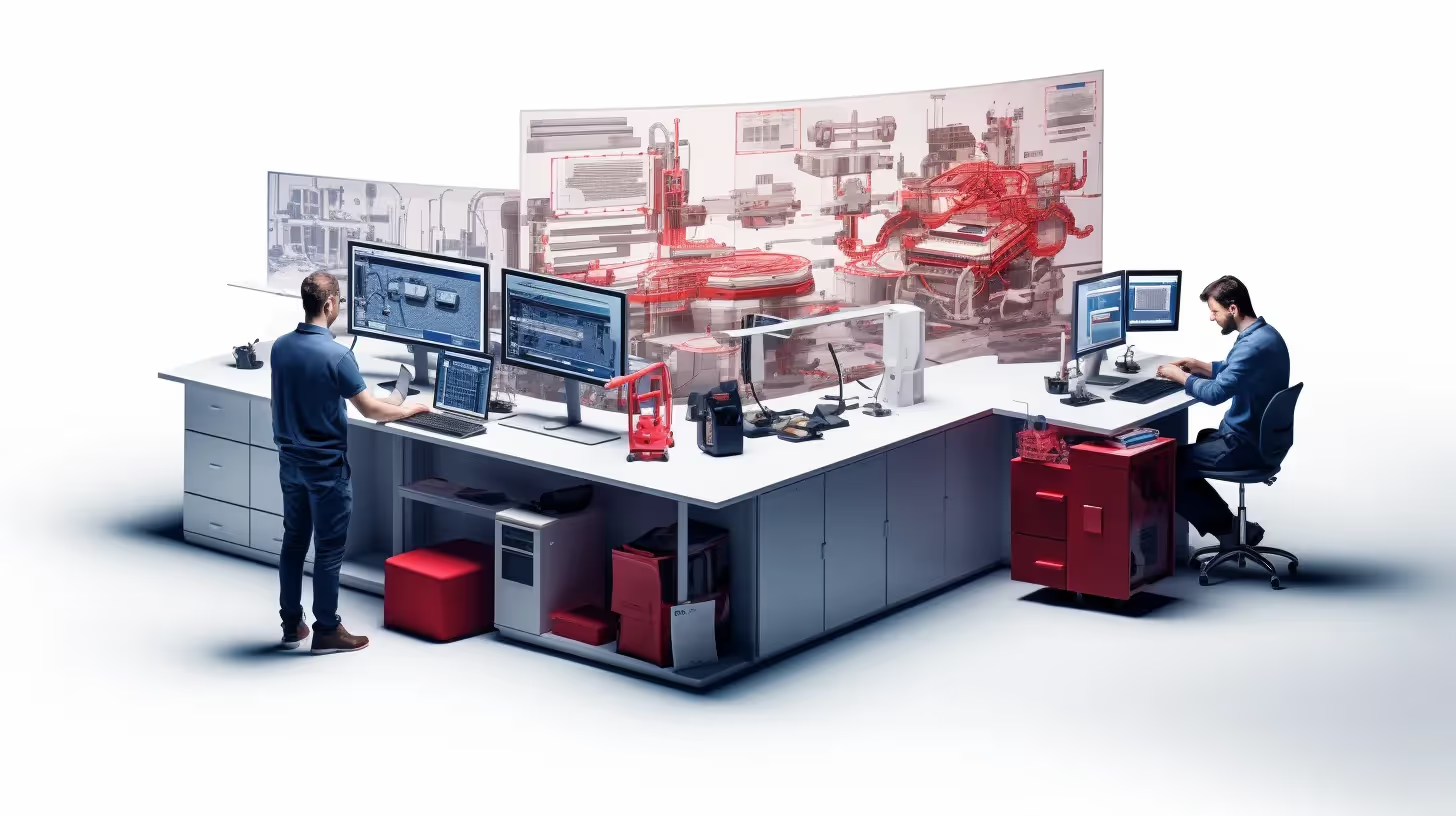
Comparing the Cost of Refurbishment and Repair
In asset management, one of the key factors that organizations consider when making maintenance decisions is cost. Understanding how refurbishment costs compare to repair is crucial for making informed choices that align with your budget and long-term asset management strategies. This article will explore the cost implications of refurbishment and repair, helping you determine the most cost-effective approach for your organization's needs.
The Cost of Refurbishment: Investment for Long-Term Value
Asset refurbishment is a comprehensive process to rejuvenate equipment to a condition that closely resembles its original state or even surpasses it. While refurbishment involves a higher upfront cost compared to repair, it offers several long-term benefits that contribute to its overall cost-effectiveness:
- Extended Lifespan: Refurbishment significantly extends the lifespan of an asset. Addressing existing issues and potential future problems reduces the frequency of replacements, saving you money in the long run.
- Performance Optimization: Upgrading components during refurbishment can improve performance and efficiency. This can result in reduced operational costs and increased productivity over the asset's extended life.
- Reduced Downtime: Refurbishment may require more extensive downtime than repair but eliminates the need for frequent, shorter repair downtime. This can lead to overall operational efficiency and cost savings.
- Environmental Responsibility: Refurbishing assets aligns with sustainability goals. Extending the equipment's life reduces the environmental impact of manufacturing and disposing of new assets.
- Maintenance Predictability: Refurbishment often includes comprehensive maintenance, reducing the need for unexpected and costly repairs over the asset's extended lifespan.
The Cost of Repair: A Short-Term Solution
Equipment repair, while generally more budget-friendly in the short term, may only sometimes be the most cost-effective option when considering the long-term perspective. Here's how the cost of repair factors in:
- Immediate Cost Savings: Repairing specific issues is usually less expensive upfront than refurbishing the entire asset. This can be advantageous when budgets are tight.
- Limited Lifespan Extension: Repairs address particular problems but may not prevent other issues from arising in the future. This can result in a higher frequency of repairs and, eventually, the need for asset replacement.
- Potentially Higher Long-Term Costs: Over time, the cumulative costs of repeated repairs, maintenance, and eventual replacement can surpass the initial refurbishment cost.
- Downtime Costs: While repairs often involve shorter downtime periods, the frequent need for repairs can add up in terms of operational disruptions and associated costs.
Making Informed Decisions: Cost Considerations
When deciding between refurbishment and repair, it's essential to consider the long-term cost implications. Here are key considerations to help you make cost-effective decisions:
- Asset Lifecycle: Assess the remaining lifecycle of the asset. Refurbishment may be more cost-effective if it's relatively young and has significant remaining potential.
- Budget Constraints: Consider your budget limitations. Repair may be a suitable short-term solution when immediate cost savings are necessary, but plan for potential refurbishment or replacement as part of long-term budgeting.
- Criticality: Evaluate how critical the asset is to your operations. Mission-critical equipment may warrant the investment in refurbishment to minimize downtime and long-term costs.
- Sustainability Goals: If sustainability is a priority for your organization, refurbishment aligns better with reducing environmental impact and is, in the long term, more cost-effective than frequent replacements.
- Performance Expectations: Determine your performance requirements. Refurbishment may provide better long-term value if you need modern capabilities and enhanced performance.
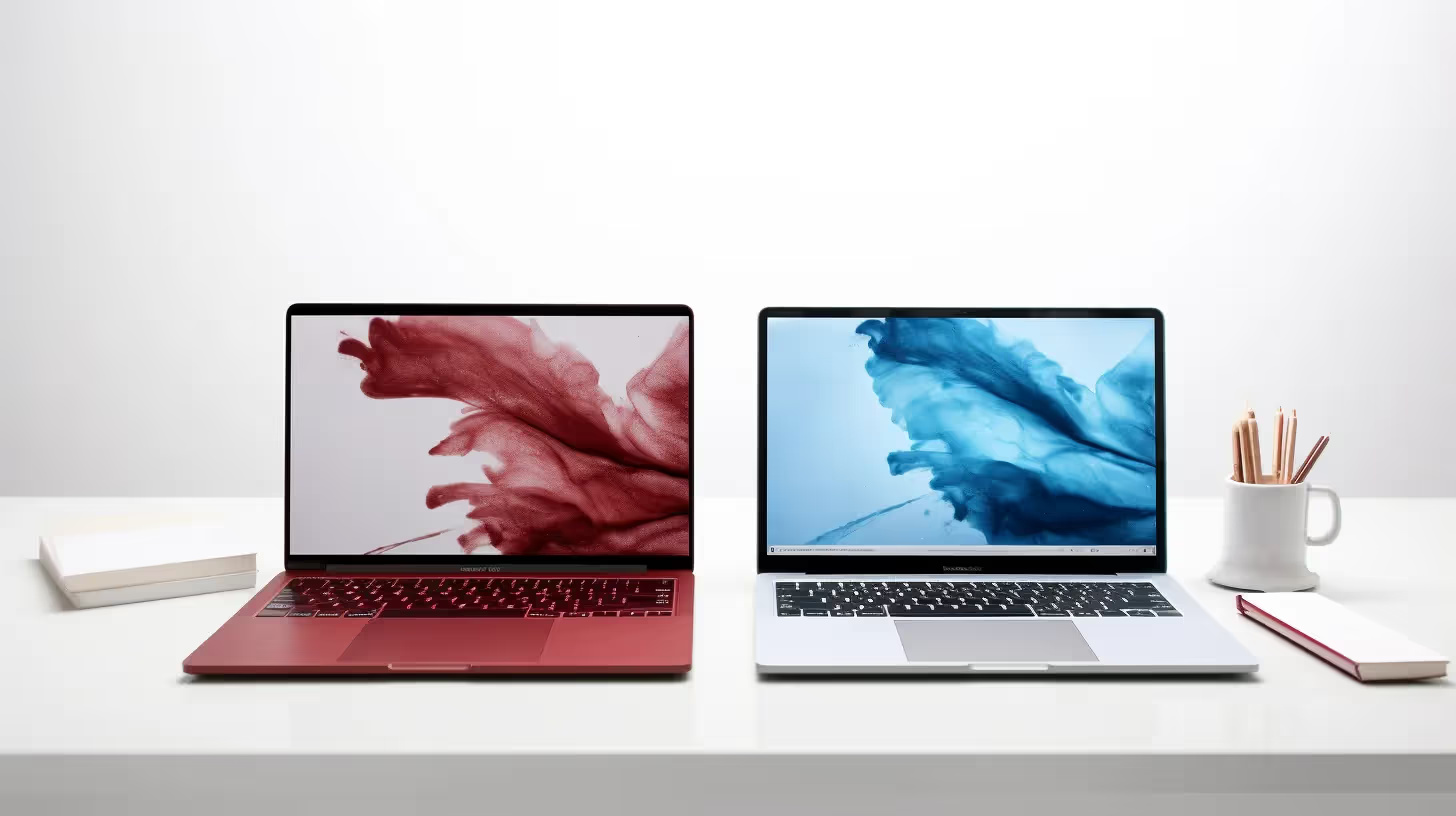
Conclusion
The choice between refurbishment and repair is far from one-size-fits-all in the complex asset management landscape. It demands careful consideration of an asset's condition, budget constraints, criticality, sustainability goals, and performance expectations. While refurbishment may entail a higher initial cost, it is often the more cost-effective and sustainable choice in the long run, extending asset lifespans, optimizing performance, and reducing overall operational costs. By making informed decisions, organizations can navigate the intricate terrain of asset management, ensuring that their investments yield maximum long-term value and efficiency.
For expert guidance on optimizing your asset management strategies, explore how UCS Logistics can assist you by visiting our website here.
Takeaways from the Article:
Asset Refurbishment vs. Repair:
Refurbishment is a comprehensive process that rejuvenates equipment to a state resembling or surpassing its original condition. It involves inspection, disassembly, replacement, cleaning, testing, and documentation.
Repair, on the other hand, is a targeted approach to address specific issues or malfunctions within an asset. It involves issue identification, component replacement, functional testing, and minimal cosmetic attention.
Benefits of Refurbishment:
Refurbishment can extend the lifespan of an asset, optimize its performance, be cost-effective in the long run, align with sustainability goals, and improve aesthetics.
Merits of Repair:
Repair is generally more budget-friendly in the short term, requires minimal downtime, and provides a focused solution to specific issues.
Decision Factors:
The choice between refurbishment and repair should be based on the asset's condition, budgetary constraints, asset criticality, sustainability goals, and performance expectations.
Cost Implications:
While refurbishment may have a higher upfront cost, it offers long-term benefits like extended lifespan, performance optimization, reduced downtime, and environmental responsibility. Repair, although less expensive initially, might lead to higher long-term costs due to frequent repairs and eventual replacement.
Reminder of the Post’s Main Point:
The decision between refurbishment and repair in asset management is crucial. While refurbishment involves a comprehensive rejuvenation of equipment, repair targets specific issues. The choice demands careful consideration of various factors, including cost, asset condition, and long-term objectives. Making informed decisions can help organizations optimize their asset value and operational efficiency.